Polysulfide Adhesive: Properties and Innovations
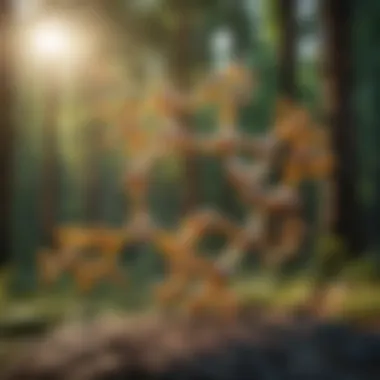
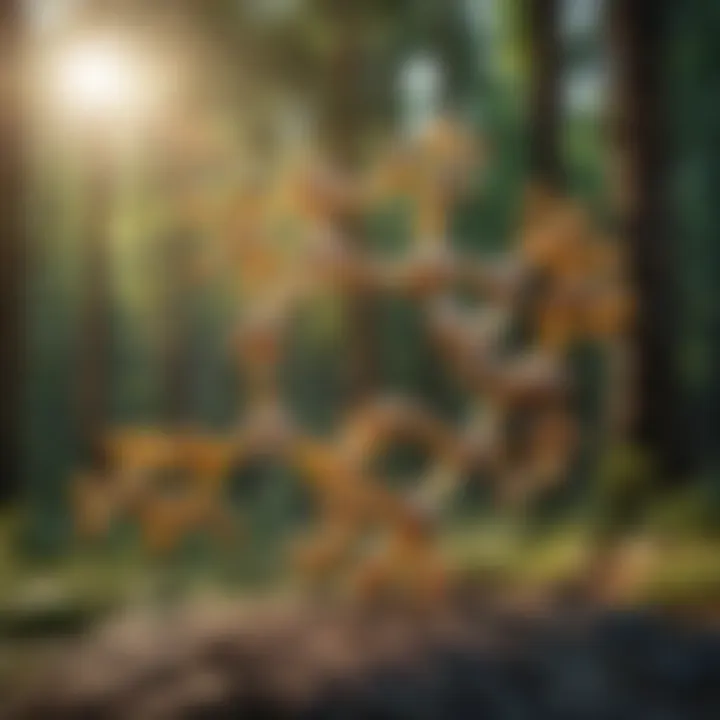
Intro
Polysulfide adhesives represent a distinct class of bonding agents that hold considerable potential across various industries, particularly in construction and manufacturing. Their unique chemical structure differentiates them from traditional adhesives, enabling stronger and more durable bonds.
This article will explore the various properties of polysulfide adhesives, examine their wide-ranging applications, and highlight recent innovations in their formulation. Understanding these aspects is essential for professionals looking to optimize adhesive use in structural contexts, ensuring longevity and performance.
By analyzing the attributes of polysulfide adhesives, we can appreciate their role in enhancing material cohesion. The forthcoming sections will dissect their specific advantages, bonding mechanisms, and response to environmental challenges. At the same time, we will touch on the regulatory landscape affecting their application and production.
The discussion aims to provide a comprehensive resource for those engaged in sectors such as forestry, construction, and manufacturing. By delving into the multi-faceted nature of polysulfide adhesives, readers will gain insights that are both practical and applicable to their respective fields.
Preamble to Polysulfide Adhesives
Polysulfide adhesives are gaining recognition in various industries due to their unique properties and versatile applications. Understanding these adhesives is crucial for professionals in construction, automotive, and aerospace, among other fields. Polysulfide adhesives offer remarkable adhesion capabilities, making them suitable for diverse materials including metals, glass, and plastics.
Their capacity to resist environmental factors, combined with their flexibility, adds significant value in applications subject to movement or thermal expansion. As markets evolve, there is a growing reliance on advanced adhesive solutions like polysulfides to meet stringent performance criteria.
Definition and Composition
Polysulfide adhesives are synthetic adhesives characterized by their unique chemical structure. They consist of long-chain polysulfide polymers that provide elasticity and strength. These adhesives are formed through the reaction of an organic polymer with sulfur, resulting in compounds that can bond effectively under varied conditions.
The composition is crucial to their performance. The backbone of polysulfide adhesives often includes repeating units of sulfur that contribute to their resilience. The flexibility allows them to endure stress and movement, making them ideal for applications where expansion and contraction occur.
History of Development
The development of polysulfide adhesives traces back to the mid-20th century when the demand for durable bonding solutions increased in aerospace and construction. Initially, their use was limited to specific high-performance applications due to complex manufacturing processes.
As technology advanced, the production of these adhesives became more streamlined. This led to wider adoption in multiple industries. Innovations in formulation have improved their effectiveness, paved the way for environmental sustainability concerns, and inspired new applications.
Overall, as markets become more competitive, understanding the evolution and potential of polysulfide adhesives is essential for continuing to harness their capabilities in modern applications.
Chemical Properties of Polysulfide Adhesives
Understanding the chemical properties of polysulfide adhesives is essential for appreciating their performance in a wide range of applications. Their unique molecular structure, curing mechanisms, and resistance to various environmental factors define their effectiveness as bonding agents. By examining these properties, one can better grasp how polysulfide adhesives excel in diverse industries such as construction, automotive, and aerospace, among others.
Molecular Structure
Polysulfide adhesives are characterized by their unique molecular architecture. Their backbone consists of alternating sulfur atoms and organic moieties. This configuration provides flexibility and allows for excellent adhesion properties. The sulfur-sulfur bonds contribute to the elasticity of these adhesives, making them suitable for dynamic environments where movement can compromise other adhesive types.
Moreover, the length of the polysulfide chain can significantly impact the adhesive's properties. Longer chains tend to enhance the adhesive strength and flexibility, while shorter chains can accelerate the curing process. Understanding the implications of molecular structure is vital for optimizing performance in specific applications.
Curing Mechanisms
The curing process of polysulfide adhesives involves a chemical reaction that transforms them from a viscous liquid to a solid state. This transformation typically occurs through exposure to moisture or heat, leading to the cross-linking of polysulfide molecules. The nature of this curing mechanism provides significant advantages. For instance, it allows for the adjustment of working time and final properties based on environmental conditions.
Additionally, polysulfide adhesives can be formulated for one-part or two-part systems. One-part systems are often more convenient for users, as they require no mixing and cure upon contact with moisture. Two-part systems, while requiring mixing prior to use, can yield superior performance due to controlled ratios of components and a more tailored curing process. Thus, understanding the curing mechanisms is crucial for selecting the appropriate system for a particular application.
Thermal and Chemical Resistance
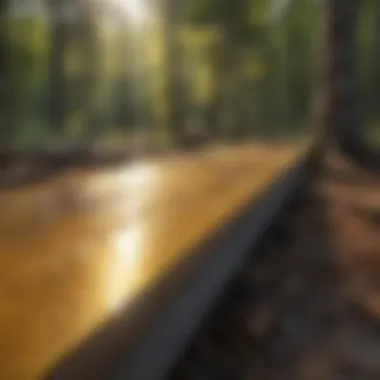
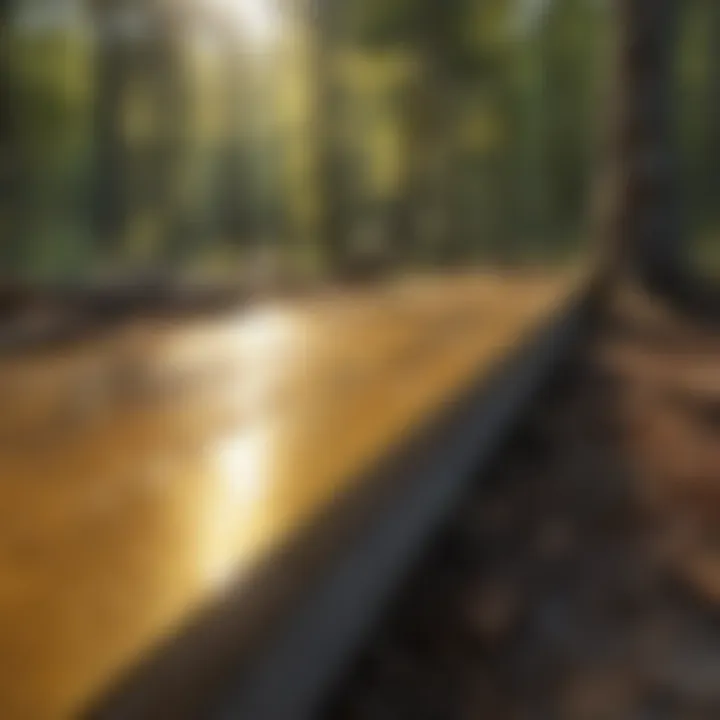
A major advantage of polysulfide adhesives is their outstanding resistance to thermal and chemical degradation. These adhesives can withstand a wide range of temperatures, which makes them suitable for high-performance applications. The thermal stability ensures that they can maintain their integrity in both extreme heat and cold, making them useful in environments like construction and aerospace, where fluctuations in temperature are common.
In terms of chemical resistance, polysulfide adhesives exhibit resilience against numerous solvents and fuels. This property is particularly beneficial in the automotive and aerospace sectors, where exposure to harsh chemicals is frequent. Their ability to maintain strength and adhesion in challenging environments enhances their appeal as bonding solutions.
"The unique properties of polysulfide adhesives allow them to thrive in demanding conditions where other adhesives might fail."
Advantages of Using Polysulfide Adhesives
Polysulfide adhesives are recognized for their superior bonding capabilities and versatile applications in diverse sectors. Their unique properties confer several advantages that are essential for both manufacturers and end-users. Understanding these benefits is crucial for optimizing the use of polysulfide adhesives in projects ranging from construction to aerospace.
Adhesion to Diverse Substrates
One of the key advantages of polysulfide adhesives is their ability to bond effectively to a wide variety of substrates. These adhesives exhibit exceptional adhesion to materials such as metals, plastics, glass, and ceramics. This versatility is particularly beneficial in industries where different materials must be joined. The chemical structure of polysulfides allows them to penetrate surface irregularities, creating a strong mechanical bond while also forming a chemical bond at the molecular level.
In applications like construction and automotive, this ability ensures the integrity of assembled components. It reduces the need for specialized adhesives for different materials, thereby streamlining the manufacturing process and reducing costs.
Flexibility and Durability
Flexibility is another significant characteristic of polysulfide adhesives. After curing, these adhesives retain a degree of elasticity. This property is advantageous in scenarios where joints may experience movements or stress. For instance, in structural applications, this flexibility helps in accommodating thermal expansion and contraction of materials, thus reducing the risk of stress fractures.
Moreover, polysulfide adhesives exhibit remarkable durability. They maintain their performance over extended periods, even under challenging environmental conditions. Their resistance to fatigue and degradation makes them a preferred choice for high-performance applications, such as those found in the aerospace and automotive sectors.
Weather and Waterproof Characteristics
Polysulfide adhesives display excellent weather and waterproof characteristics. They resist moisture, UV radiation, and temperature fluctuations. These attributes are critical for applications where exposure to harsh environmental conditions is inevitable. In the construction industry, for example, polysulfide adhesives are utilized in sealing joints in roofing and facades, ensuring durability and longevity of structures.
Additionally, their waterproof feature makes them ideal for applications in marine environments or areas prone to water exposure. The ability to maintain bond strength and performance in wet conditions enhances their utility in various fields, ensuring reliability in structural integrity and product performance.
Polysulfide adhesives are not only versatile but also reliable in extreme conditions, making them vital for modern engineering and manufacturing.
In summary, the advantages of polysulfide adhesives lie in their wide-ranging applicability, durability, and resilience against environmental challenges. These properties provide significant benefits for industries that require high-performance bonding solutions.
Applications in Various Industries
The applications of polysulfide adhesives span multiple industries, highlighting their significance in modern manufacturing and construction practices. These adhesives are not merely an option; they are often the preferred choice due to their unique properties, which include flexibility, durability, and strong adhesive qualities. Each industry has its specific demands, and polysulfide adhesives meet various needs effectively.
Construction and Infrastructure
In the construction field, polysulfide adhesives are widely used for sealing and bonding elements such as precast concrete panels and structural components. One reason for their popularity is their ability to accommodate movement, which is crucial in structural applications. The flexibility of these adhesives allows them to absorb stress from temperature fluctuations and vibrations without losing bond integrity.
Furthermore, the durability of polysulfide adhesives extends the lifespan of construction materials, reducing the need for frequent repairs. Their excellent resistance to water and chemicals also makes them ideal for use in environments exposed to harsh weather conditions. Ensuring the quality of infrastructure relies on effective adhesive solutions, making polysulfide adhesives an essential component in modern building techniques.
Automotive Industry
The automotive industry demands high-performance adhesives that can withstand extreme conditions. Polysulfide adhesives meet these requirements, making them valuable in assembling various vehicle components. These adhesives are known for their strong bond to metals, plastics, and composites, ensuring durability in critical automotive applications.
Additionally, polysulfide adhesives contribute to vehicle safety by providing structural integrity and reducing noise and vibration. They are especially useful in sealing seams and joints in body panels and windshields. The automotive sector continually seeks ways to enhance vehicle design and efficiency, and polysulfide adhesives play a vital role in these advancements.
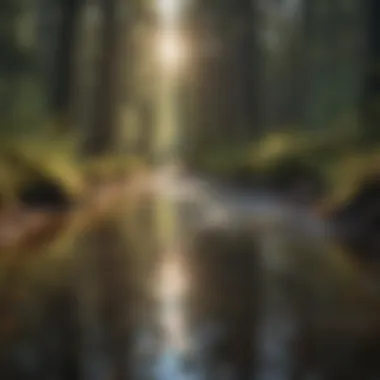
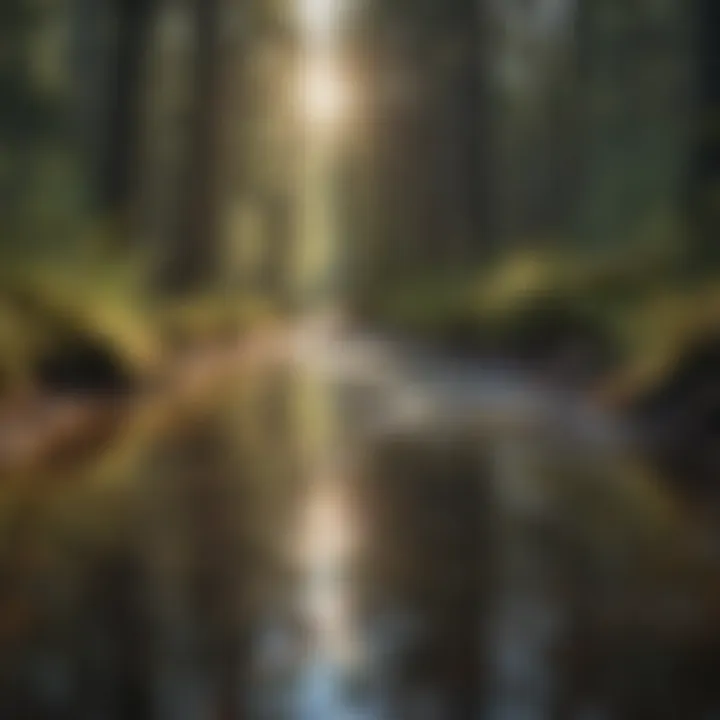
Aerospace Applications
Aerospace applications require adhesives that can endure severe temperatures and pressures. Polysulfide adhesives have been adapted for this high-stakes environment, providing reliable performance in assembling aircraft components. Their weight-to-strength ratio is beneficial, allowing for lightweight constructions without compromising safety or performance.
The ability to withstand fuel exposure and other aggressive chemicals further enhances their suitability for aerospace usage. These adhesives can be used in applications ranging from bonding structural elements to sealing fuel tanks, proving they are integral to aerospace engineering advancements.
Electrical and Electronics
In the electrical and electronics industry, polysulfide adhesives serve critical functions such as insulating and sealing electronic components. Their resistance to moisture and chemicals helps protect sensitive parts from damage, ensuring longevity and reliability. The electrical properties of these adhesives allow for safe assembly of devices needing tight tolerances and secure connections.
The versatility in applications in this field demonstrates how polysulfide adhesives can address both mechanical and electronic needs effectively. As technology progresses, the reliance on robust adhesive solutions will likely increase, solidifying the role of polysulfide adhesives in this sector.
Environmental Considerations
The relationship between polysulfide adhesives and the environment has garnered significant attention, particularly given the increasing demand for sustainable materials. In this section, we will explore the sustainability of polysulfide materials and address the recyclability and end-of-life issues associated with their use. This is crucial for professionals in forestry, construction, and manufacturing to understand how these adhesives can impact their industry and contribute to environmental objectives.
Sustainability of Polysulfide Materials
Polysulfide adhesives can be regarded as a sustainable choice when evaluated through various environmental metrics. Their unique chemical structure confers several advantages that contribute to sustainability goals, including lower emissions during production. These adhesives often utilize by-products from other industrial processes, thus minimizing waste.
Moreover, polysulfide adhesives exhibit a long life span, leading to reduced frequency of replacement and less material waste when compared to alternatives. Following the principles of green chemistry, these adhesives can effectively bond a myriad of substrates without requiring extensive preparatory processes, which often consume additional energy and generate more pollutants.
However, it is essential to consider the sourcing of raw materials. Employing sustainable practices in the extraction and processing of chemicals used to create polysulfides can enhance the overall sustainability profile of these materials. Efforts to refine processes, such as using bio-derived components, can further reduce their ecological footprint.
Recyclability and End-of-Life Issues
The recyclability of polysulfide adhesives presents both challenges and opportunities for improvement. While the high performance of these adhesives is undeniable, their chemical composition often complicates post-consumer recycling efforts. Many disposal facilities are not equipped to process these materials, leading to potential environmental hazards when they end up in landfills.
To address this issue, some industry innovations focus on creating formulations that can be recycled. This shift towards circular economy principles includes reclaiming and reusing components wherever feasible. Education for consumers and manufacturers can play a vital role in improving the end-of-life management of polysulfide adhesives. Encouraging correct disposal practices and establishing dedicated recycling streams is essential for minimizing their environmental impact.
As more attention is drawn to environmental regulations, the pressure on manufacturers to develop sustainable adhesive solutions increases. Subsequently, investing in research and development, to innovate in the area of recyclability and to find alternative formulations, is not just beneficial but necessary for future market success.
"Sustainable practices are not merely a trend; they are rapidly becoming a necessity in all manufacturing sectors."
In summation, the environmental considerations surrounding polysulfide adhesives are pivotal as industries strive for sustainability. Understanding their sustainable attributes and tackling recyclability will set the stage for more environmentally responsible choices in the adhesive market.
Regulatory Standards and Compliance
The area of regulatory standards and compliance is crucial in the context of polysulfide adhesives. Companies need to adhere to various guidelines and industry standards to ensure both product effectiveness and safety. This not only helps in establishing trust with clients but also aligns with environmental regulations. As such, understanding these standards is vital for professionals in fields that use polysulfide adhesives.
Industry Standards for Adhesives
Adhesives, particularly polysulfide types, must comply with industry-specific standards. These guidelines offer a framework for evaluating adhesive performance. Common standards may include ISO, ASTM, and other international specifications that outline testing methods, quality control, and consistency.
- ISO 14001: Focuses on environmental management ensuring that products do not adversely impact the environment.
- ASTM D-1002: Measures adhesive strength under specific conditions.
- EN 204: Designates durability and performance attributes for adhesives used in wood.
Complying with these standards indicates that the adhesive meets quality requirements and assures users of its reliability across various applications, from construction to aerospace.
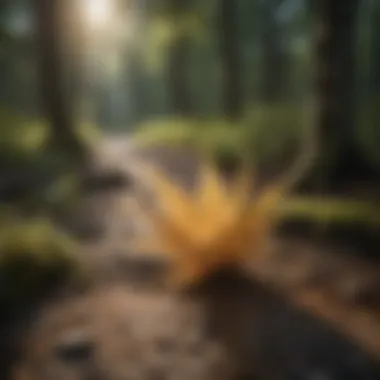
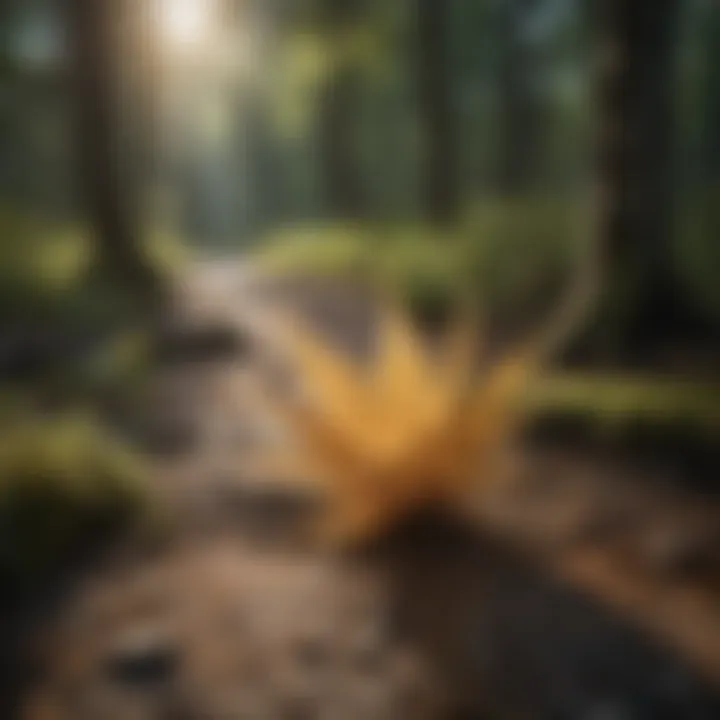
Health and Safety Regulations
The health and safety regulations surrounding polysulfide adhesives address both the manufacturing process and end-use applications. These regulations ensure that products do not pose risks to human health, either through inhalation of fumes or skin exposure. Relevant standards include:
- OSHA guidelines: Set workplace safety standards regarding hazardous materials.
- REACH regulation: Focuses on the safe use of chemical substances in EU countries.
- Material Safety Data Sheets (MSDS): Provide detailed information on handling, hazards, and first aid measures associated with the adhesive.
Compliance with such regulations not only meets legal requirements but also enhances workplace safety by minimizing risk.
It is essential for manufacturers and users to be aware of these standards and regulations to maintain industry compliance and promote safety.
Ensuring regulatory compliance for polysulfide adhesives fosters market competitiveness and trust among stakeholders.
Recent Innovations in Polysulfide Adhesives
Recent innovations in polysulfide adhesives are significant because they enhance the performance and broaden the applications of these materials in various industries. Companies and researchers are pushing the boundaries to improve formulation technologies and adapt to the evolving needs of different sectors, ensuring that polysulfide adhesives remain a reliable choice.
Advancements in Formulation Technology
Innovations in formulation technology have led to improvements in the chemical composition of polysulfide adhesives, making them more versatile and efficient. These advancements often focus on optimizing the balance between adhesion strength and flexibility, which is critical in applications where movement or temperature changes occur. New additives and modifiers are also being introduced to enhance bonding capabilities.
These formulations can improve curing times, reducing the wait for a bond to solidify. Some recent developments include the use of silane coupling agents, which improve the adhesive's performance on various substrates, offering better adhesion on surfaces that traditionally posed challenges. Furthermore, using eco-friendly raw materials in formulations is becoming more common, contributing to sustainability goals.
Nanocomposite Enhancements
Another area of innovation is the incorporation of nanocomposite materials into polysulfide adhesives. These enhancements provide dramatic improvements in mechanical properties and thermal stability. Nanoparticles, such as silica or carbon nanotubes, are added to the adhesive matrix, resulting in a product that exhibits superior performance characteristics.
- Improved Strength: The mechanical strength of polysulfide adhesives can significantly increase, making them more suitable for demanding applications.
- Enhanced Resistance: The addition of nanocomposites can offer better resistance to harsh environmental conditions.
- Reduced Weight: These innovations often allow for lighter materials without sacrificing performance, appealing to industries like automotive and aerospace where weight reduction is crucial.
Polysulfide adhesives with nanocomposite enhancements are leading to more durable and effective solutions across industries.
In summary, the recent innovations in polysulfide adhesives, particularly in formulation technology and nanocomposite inclusion, point towards a future where these adhesives play an even more critical role in diverse applications. Industries looking for reliable and advanced adhesion solutions will find that polysulfide adhesives continue to evolve, meeting their expectations.
Future Trends in Polysulfide Adhesive Applications
Future trends in polysulfide adhesive applications signify an important evolution in material science that caters to the needs of diverse industries. As environmental challenges continue to grow, the demand for more sustainable and efficient adhesive solutions has triggered innovation. This section discusses market outlook, growth projections, and the potential for new applications within this realm.
Market Outlook and Growth Projections
The market for polysulfide adhesives shows a promising outlook. According to industry reports, the global polysulfide adhesive market is projected to expand significantly in the coming years. Factors contributing to this growth include:
- Increasing Demand in Construction: With rapid urbanization, the construction industry seeks reliable adhesive solutions. Polysulfide adhesives fulfill this need with their strong bonding capabilities.
- Automotive Advancements: Innovations within the automotive sector are driving the requirement for high-performance adhesives. Polysulfide adhesives provide durability under extreme temperatures, making them suitable for use in automotive applications.
- Regulatory Compliance: Regulations focusing on environmental standards have prompted industries to adopt more eco-friendly materials. Polysulfide adhesives, known for their lower environmental impact, are increasingly favored.
Forecasted growth rates suggest that polysulfide adhesives will gain a larger market share as more industries recognize their advantages.
Potential for New Applications
The versatility of polysulfide adhesives opens the door to various new applications. Their unique properties provide opportunities that include:
- Marine Industry: The marine sector is beginning to utilize polysulfide adhesives for their water-resistant and flexible properties. Applications in boat manufacturing and repairs are expected to rise.
- Medical Devices: As medical technology advances, polysulfide adhesives may find roles in the production of disposable medical devices that require strong yet flexible seals.
- Wind Energy: In the renewable energy sector, polysulfide adhesives are considered for use in wind turbine construction, where durability and resistance to chemical exposure are crucial.
The ability to enhance performance through innovations will facilitate these potential applications.
In summary, the future for polysulfide adhesives appears bright. As industries evolve, the demand for advanced adhesive solutions grows. This poses both challenges and opportunities for innovation, pushing the boundaries of what polysulfide adhesives can achieve.