Understanding the Manufacturing Carbon Footprint
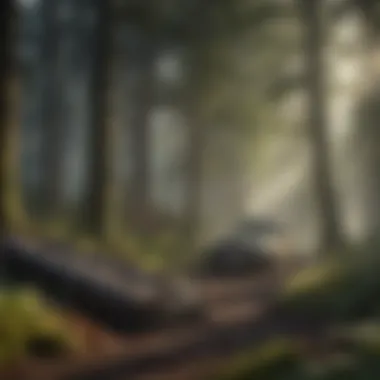
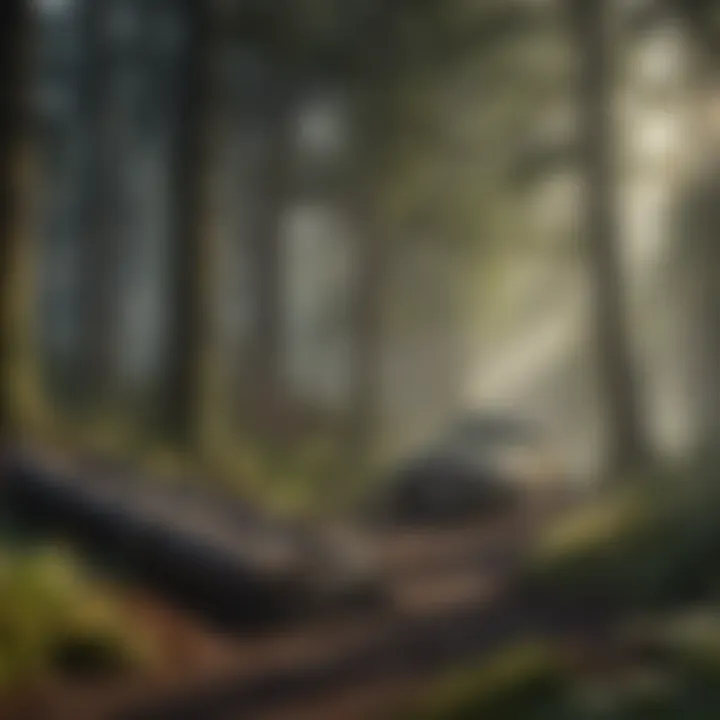
Intro
The impact of manufacturing on the environment is significant. The concept of a manufacturing carbon footprint is central to understanding this impact. It relates to the total greenhouse gas emissions produced during the manufacturing of goods. This includes every stage of the process, from resource extraction to production and distribution. Understanding this footprint is vital for promoting sustainability in modern industry.
This article provides an in-depth analysis of the manufacturing carbon footprint, focusing on its implications for businesses, consumers, and policymakers. By dissecting the various elements involved in the manufacturing process, it seeks to clarify the key sources of carbon emissions and discusses ways to effectively measure and mitigate these emissions.
Moreover, this discussion will explore how technology, policy, and industry standards can influence a more sustainable manufacturing environment. As awareness of sustainability increases, understanding and improving the carbon footprint becomes an essential responsibility for all involved in the manufacturing sector.
Understanding Manufacturing Processes
A. Key Components of Manufacturing
Manufacturing processes comprise several stages, each contributing to the overall carbon footprint. The stages include:
- Resource Extraction: This involves the collection of raw materials, often resulting in significant emissions due to transportation and energy use.
- Production: The manufacturing phase itself typically has the highest emissions. Energy-intensive operations contribute prominently to the carbon footprint.
- Distribution: Transporting finished goods adds further emissions, influenced by the mode of transport and distance.
B. Importance of Measuring Carbon Emissions
Accurate measurement of carbon emissions at each stage is vital. It helps businesses identify where reductions can be made. Many companies are beginning to utilize tools like carbon footprint calculators. These tools provide valuable data that can inform decision-making.
“Understanding the details of your carbon emissions enables a more targeted strategy for reduction.”
Technological Impact on Reduction Efforts
A. Innovations in Manufacturing Technology
Technological advances play a crucial role in reducing the carbon footprint. Some effective technologies include:
- Energy-efficient machinery: New machines consume less power and reduce waste.
- Renewable energy sources: Utilizing solar, wind, or hydroelectric power can drastically lower emissions.
- Automation: Streamlining processes often leads to less energy consumption.
B. Policy Support for Technology Integration
Regulatory frameworks can encourage or mandate the use of eco-friendly technologies. Governments worldwide are increasingly setting policies aimed at curbing emissions in manufacturing. This support can drive industries to adopt innovative solutions.
Epilogue
Addressing the manufacturing carbon footprint involves a comprehensive understanding of the processes involved, the key sources of emissions, and the application of effective technology and policies. All stakeholders in the manufacturing chain, from producers to consumers, play a role in promoting sustainability and reducing their carbon footprint.
Understanding the Manufacturing Carbon Footprint
The manufacturing carbon footprint refers to the total greenhouse gas emissions associated with the manufacturing processes, from raw material extraction to distribution and consumption of products. Understanding this concept is crucial for anyone involved in manufacturing, as it helps identify the sources of emissions and the potential impact on climate change.
The manufacturing sector significantly contributes to global carbon emissions. For instance, industries such as steel, cement, and textiles are known for their high energy consumption and emissions. By measuring their carbon footprint, organizations can take meaningful steps towards sustainability.
Measuring the carbon footprint aids companies in recognizing areas where they can improve their operations. It allows them to set targets for emission reductions, report their findings transparently. Additionally, it fosters a culture of responsibility among employees, stakeholders, and consumers. Recognizing the value of an environmentally friendly approach can also enhance a company's reputation.
The journey toward a sustainable manufacturing footprint involves a detailed understanding of its components. This knowledge not only positions businesses to optimize their processes but also aligns them with evolving regulations and consumer expectations regarding sustainability.
Definition and Explanation
A manufacturing carbon footprint is defined as the sum total of greenhouse gas emissions directly and indirectly linked to the production of goods. This encompasses emissions from various stages, including:
- Raw material extraction: The process of obtaining raw materials often entails energy-intensive operations, leading to significant emissions.
- Manufacturing processes: The energy used in factories contributes heavily to the carbon footprint. Processes such as mixing, assembly, and finishing require substantial energy.
- Transportation: Moving products from facilities to consumers is another contributor. This includes the emissions related to transporting raw materials and finished products.
Understanding these definitions provides a backdrop for evaluating emission sources, which is essential for effective management and reduction strategies.
Importance of Measuring Carbon Footprint
Measuring the carbon footprint serves several critical purposes in the context of manufacturing:
- Identifying Emission Sources: Accurate measurement helps spot specific areas or processes where emissions are the highest, allowing for targeted interventions.
- Regulatory Compliance: Many regions have established regulations requiring businesses to monitor and report carbon emissions. Compliance can mitigate legal risks and potential fines.
- Cost Reduction: Implementing carbon footprint measurement practices can uncover inefficiencies. Reducing emissions often leads to lower energy consumption, which translates to cost savings.
- Enhancing Brand Value: Companies perceived as environmentally responsible can attract consumers who prioritize sustainability. This can lead to increased customer loyalty and market share.
- Driving Innovation: Organizations that measure their carbon footprint are often more motivated to innovate. This may include exploring new technologies, energy-efficient processes, or sustainable materials.
"Companies that take a proactive approach to understanding their carbon emissions position themselves as leaders in sustainability."
Components of the Manufacturing Carbon Footprint
Understanding the components that contribute to the manufacturing carbon footprint is critical. This understanding allows companies to effectively strategize on reducing emissions and improving sustainability practices. The carbon footprint in manufacturing largely consists of direct and indirect emissions, insights from life cycle assessments, and a thorough analysis of energy consumption. Each of these elements plays a distinctive role in painting a holistic picture of a company's environmental impact.
Direct vs. Indirect Emissions
Direct emissions arise from sources that are owned or controlled by the organization. For example, emissions from fossil fuels burned in manufacturing equipment are considered direct. These emissions are often easier to identify and quantify due to their measurable nature. In contrast, indirect emissions occur as a consequence of the activities of the organization but are from sources not owned or controlled by it. This includes emissions from the production of purchased materials and transportation of goods. Addressing both types of emissions is vital because they collectively encompass the full scope of a manufacturing operation's carbon footprint.
To effectively reduce carbon emissions, manufacturers need to:
- Identify sources of direct emissions within their operations.
- Collaborate with suppliers to identify and minimize indirect emissions.
- Implement tracking systems to measure both types, as this data is essential for decision-making and reporting.
Life Cycle Assessment
Life cycle assessment (LCA) is a comprehensive method used to evaluate the environmental impacts associated with all the stages of a product's life, from raw material extraction through production and use, to disposal. This assessment provides critical insights into which stages are contributing the most significantly to the carbon footprint. LCA can reveal opportunities for improvement that may not be immediately obvious without a systematic approach.
The process includes:
- Goal and Scope Definition: Clarifying the purpose of the assessment and the product or service being analyzed.
- Inventory Analysis: Quantifying energy and materials for each phase of the product's lifecycle.
- Impact Assessment: Evaluating potential environmental impacts.
- Interpretation: Analyzing the findings to identify opportunities for reduction.
Incorporating LCA into manufacturing strategies leads to sustainable design choices and ultimately lowers the carbon footprint.
Energy Consumption Analysis
Energy consumption is a significant contributor to carbon emissions in manufacturing. Assessing energy use patterns helps organizations understand their dependence on different energy sources, including renewables and non-renewables. A thorough energy consumption analysis focuses on:
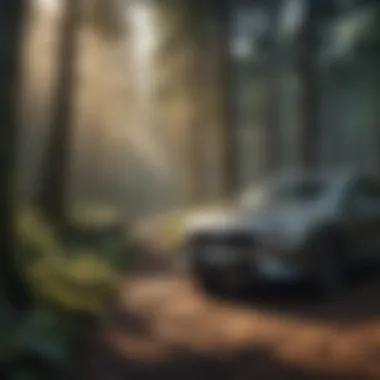
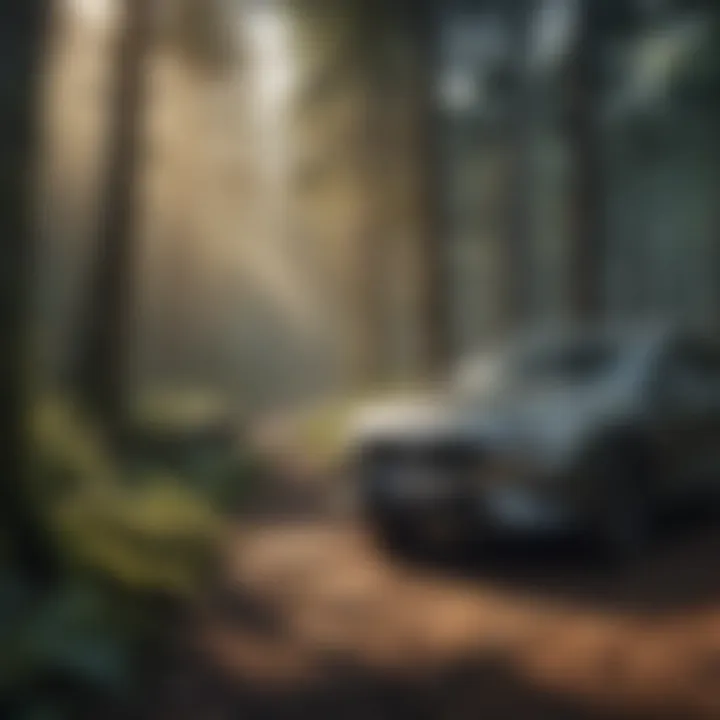
- Identifying energy-intensive processes.
- Benchmarking consumption against industry standards.
- Assessing the carbon intensity of energy sources utilized.
By optimizing energy efficiency, manufacturers can significantly reduce both operational costs and their carbon footprint. Steps to improve energy consumption include:
- Upgrading to energy-efficient machinery.
- Implementing energy management systems.
- Encouraging behaviors that conserve energy among employees.
Through the detailed examination of these key components, manufacturers can identify critical areas for improvement. This initiative not only enhances operational efficiency but also contributes to a more sustainable future.
Measuring the Carbon Footprint
Measuring the carbon footprint in manufacturing is crucial for understanding the environmental impact of industrial operations. By quantifying emissions, businesses can identify key areas for improvement and develop strategies to reduce their carbon footprint. This measurement provides a baseline which allows companies to track their progress over time. Furthermore, it aids in complying with regulations and meeting customer expectations for sustainability. Accurate measurement ultimately supports informed decision-making, fostering a culture of accountability and responsibility in the manufacturing sector.
Tools and Methodologies
Various tools and methodologies exist for effectively measuring the carbon footprint. Organizations often employ software solutions such as SimaPro or GaBi to conduct Life Cycle Assessments (LCAs). These tools enable users to analyze environmental impacts across different stages of production. Additionally, frameworks like the Greenhouse Gas Protocol offer standardized approaches for calculating emissions. Using these methodologies helps ensure the consistency and credibility of results.
Key methodologies include:
- Quantitative Analysis: This involves the collection of data to compute emissions based on direct and indirect sources.
- Qualitative Assessments: These may include stakeholder surveys and expert opinions that provide context to numerical data.
- Modeling Techniques: Emission factors and models can estimate potential emissions for various scenarios.
By using a combination of these methodologies, companies can develop a more holistic understanding of their carbon footprint.
Data Collection Techniques
Accurate data collection is foundational in measuring the carbon footprint. Several approaches can be utilized. Companies often gather data from operational records, supplier reports, and direct observations. Some key techniques include:
- Surveys and Questionnaires: Engaging employees and suppliers through surveys can yield valuable insights into emissions associated with specific processes.
- Monitoring Systems: Automated systems can continuously gather data on energy usage and emissions.
- Remote Sensing and IoT Devices: These technologies enable real-time monitoring of emissions, providing a more comprehensive view of the manufacturing process.
Additionally, using standardized reporting frameworks can enhance the consistency of data collection and engagement with stakeholders.
Challenges in Measurement
While measuring the carbon footprint is essential, numerous challenges arise during the process. Notably, the lack of standardized data across industries complicates comparisons and analyses. Companies may also struggle with:
- Data Quality Issues: Inconsistent or incomplete data can lead to inaccurate assessments of emissions.
- High Costs of Measurement: Implementing comprehensive measurement frameworks may require significant financial investments, which can be a barrier for smaller manufacturers.
- Complex Supply Chains: For organizations with intricate supply chains, attributing emissions to a specific product or process can be daunting.
Moreover, regulatory compliance can add additional layers of complexity, as businesses must navigate differing requirements across regions and jurisdictions.
"Accurate measurement of the carbon footprint is the first step towards meaningful reduction strategies. Without reliable data, any efforts may lack direction or effectiveness."
Key Sources of Carbon Emissions in Manufacturing
Understanding the key sources of carbon emissions in manufacturing is essential for addressing environmental concerns. This segment helps to identify where emissions occur, allowing for more effective mitigation strategies. Recognizing these sources not only contributes to sustainable practices but also enhances operational efficiency and may reduce costs in the long run.
Raw Material Extraction
The extraction of raw materials is often the first step in the manufacturing cycle. This phase can be highly carbon-intensive, especially for industries relying on fossil fuels and metals. For example, the mining processes for metals like aluminum require significant energy, primarily derived from non-renewable sources. This leads to large volumes of CO2 emissions, contributing to the overall carbon footprint of manufacturing operations.
Various methods used in raw material extraction, such as strip mining or open-pit mining, also result in habitat destruction and pollution, impacting biodiversity and ecosystems. Moreover, transporting extracted materials to factories further elevates carbon outputs. Therefore, mitigating emissions at this stage can have profound ecological and economic benefits. Encouraging the use of recycled materials and responsible sourcing can lead to lower emission rates.
Manufacturing Processes
Following raw material extraction, manufacturing processes have a direct impact on the carbon footprint of product creation. Different methods of production, such as welding, molding, and assembly, differ in their energy requirements. High-temperature processes or those using fossil fuel-based equipment result in elevated emissions.
Applying energy-efficient technologies in manufacturing can significantly reduce emissions. For example, automating processes can optimize energy use, while adopting efficient machinery can minimize waste. Additionally, manufacturers can explore alternative processes that rely on renewables or less carbon-intensive methods. Training employees in sustainable practices also enhances awareness and encourages emission reductions at the workplace.
Transportation and Distribution
Transportation represents another significant contributor to the manufacturing carbon footprint. The logistics of moving materials to and from facilities are determined by various factors, including distance, mode of transport, and type of goods.
For instance, trucks and ships often use diesel, a fossil fuel that emits considerable amounts of CO2. To lessen transportation emissions, companies can convert fleets to electric-powered vehicles or consider optimizing routes to reduce travel distances. Investing in local supplies will decrease the need for lengthy transportation, further lessening carbon outputs.
"Mitigating emissions is often most effective when addressing multiple sources simultaneously. A comprehensive approach yields the best results."
Strategies for Reducing the Carbon Footprint
Reducing the carbon footprint in manufacturing is essential for sustainability and long-term ecological balance. The strategies to achieve this reduction need to be multifaceted, addressing various aspects from energy consumption to waste management. Implementing effective strategies can lead to significant cost savings and improved brand reputation. The importance of reducing carbon emissions cannot be overstated; it plays a critical role in combating climate change, which is a significant global challenge today.
Energy Efficiency Improvements
Energy efficiency improvements are vital for lowering the carbon footprint in manufacturing. By optimizing energy use, companies can reduce greenhouse gas emissions while also cutting costs. This can be achieved through several methods:
- Upgrading Equipment: Replacing outdated machinery with energy-efficient models can have a significant impact. Modern equipment often uses advanced technologies that consume less energy.
- Process Optimization: Analyzing and adjusting manufacturing workflows can reveal inefficiencies. Streamlining processes can minimize energy waste and improve overall productivity.
- Employee Training: Educating workers about energy-saving practices can lead to a more conscious workplace. When staff understand how their actions affect energy consumption, they can adopt more sustainable habits.
Investing in these improvements typically yields a strong return on investment. Companies may also benefit from incentives and tax breaks provided by governments for adopting energy-efficient practices.
Switching to Renewables
Switching to renewable energy sources is another critical strategy. Fossil fuels are a primary contributor to carbon emissions in manufacturing. Here are some ways to transition towards renewable energy:
- Solar Energy: Installing solar panels can provide a sustainable energy source. Although upfront costs can be high, long-term savings and energy independence make it worthwhile.
- Wind Energy: Utilizing wind turbines can also generate significant power. Industries located in areas with strong winds may find this option particularly beneficial.
- Biomass and Hydropower: These sources can present solutions for certain manufacturing processes, depending on geographic and operational contexts.
Transitioning to renewable sources not only lowers emissions but also enhances a company's public image. It might attract customers who prioritize sustainability in their purchasing decisions.
Waste Management Practices
Effective waste management practices play a critical role in minimizing the carbon footprint. Manufacturing processes generate considerable waste, and how this is managed can lead to significant emissions. Important strategies include:
- Recycling and Reusing: Implementing systems to recycle materials can reduce the demand for raw resources. This lowers the emissions associated with production and waste disposal.
- Composting Organic Waste: For companies that produce organic waste, composting can offer an environmentally-friendly disposal method. It diverts waste from landfills and contributes to soil health.
- Adopting Circular Economy Principles: This approach emphasizes keeping resources in use for as long as possible. By designing products for longevity and ease of repair, manufacturers can minimize waste.
Moreover, effective waste management can lead to economic benefits. By reducing waste, companies often find that they can lower disposal costs, further cementing their financial and environmental commitment.
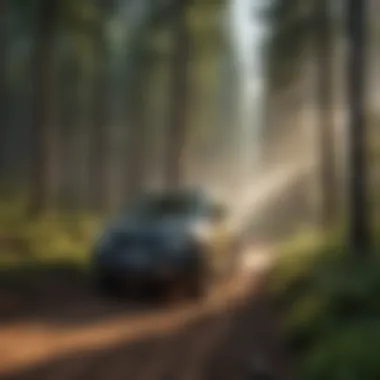
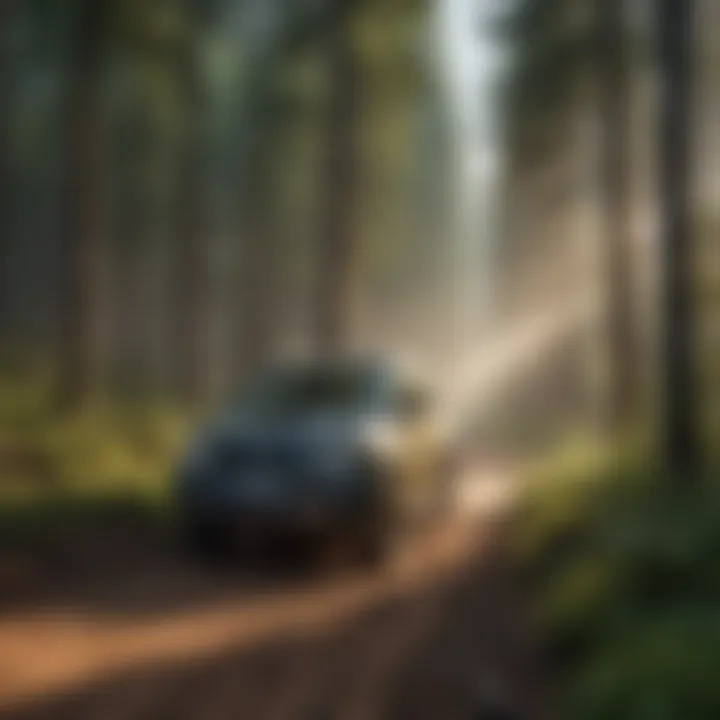
"Investing in sustainable practices can lead to cost savings, improved efficiency, and a positive public perception."
By implementing these strategies, manufacturers can pave the way towards a more sustainable future. It is crucial for businesses to evaluate their current practices and take actionable steps toward reducing their carbon footprint.
Technological Innovations in Manufacturing
Technological innovations play a crucial role in transforming manufacturing processes, especially in the context of reducing the carbon footprint. They present significant opportunities to enhance efficiency, optimize resource usage, and minimize waste. This integration not only underscores environmental responsibility but can also lead to cost savings and improved market competitiveness for businesses. As industries move towards sustainability, embracing these innovations becomes imperative.
Automation and AI
Automation and artificial intelligence (AI) are reshaping manufacturing landscapes. Automated systems can operate machinery with precision and consistency, leading to reduced energy consumption and lower emissions compared to traditional methods. AI can analyze vast datasets to identify areas for improvement, manage supply chains efficiently, and forecast demand more accurately. This intelligent system can adjust processes dynamically, leading to less material usage and waste.
Moreover, automation technologies can significantly lower labor-related emissions by enhancing efficiency. Tasks that are repetitive or hazardous for human workers can be handled by machines, decreasing the overall exposure to risky situations and physical demands on employees. In this way, the manufacturing sector can become more sustainable while maintaining worker safety.
Carbon Capture and Storage
Carbon capture and storage (CCS) technologies offer a pathway to mitigate carbon emissions from manufacturing processes. These technologies work by capturing CO2 emissions produced from industrial processes and securely storing them underground or repurposing them for other uses. This approach is particularly relevant for industries with high emissions, such as cement and steel production.
The implementation of CCS can support compliance with environmental regulations while enabling companies to meet sustainability goals. However, it's essential to acknowledge that CCS is not a standalone solution. It must be integrated with other strategies aimed at emissions reduction, such as transitioning to renewable energy sources. This combination can lead to substantial reductions in carbon footprints in manufacturing sectors.
Sustainable Materials Development
Sustainable materials development involves designing and utilizing materials that have minimal negative impacts on the environment throughout their life cycle. This includes considering resource extraction, production processes, usage, and disposal. Innovations in this area include biodegradable materials and those with lower energy footprints during their production.
Developing such materials not only contributes to carbon footprint reduction but can also satisfy increasing consumer demands for environmentally friendly products. For instance, biodegradable plastics can replace conventional plastics in many applications, thus decreasing the overall waste in landfills. By aligning product development with sustainability goals, manufacturers can enhance brand reputation and develop new markets.
"The adoption of sustainable materials is essential for any manufacturing operation aiming at reducing its carbon footprint while meeting contemporary environmental expectations."
In summary, technological innovations such as automation, CCS, and sustainable materials development are vital for the manufacturing sector's evolution towards sustainability. They facilitate emissions reduction and enhance operational efficiency, offering multiple benefits for companies willing to invest in them.
Policy and Regulatory Framework
The policy and regulatory framework plays a critical role in shaping the manufacturing sector's approach to carbon footprint mitigation. Governments and regulatory bodies are essential in establishing guidelines that encourage sustainable practices while holding businesses accountable for their environmental impact. These regulations often aim to reduce greenhouse gas emissions, promote energy efficiency, and enhance overall sustainability in manufacturing processes.
Governments can implement policies that influence production methods. These policies may include emissions trading schemes, carbon taxes, and environmental standards that necessitate compliance from manufacturers. When organizations understand the legal landscape, they can better strategize to meet or exceed the established environmental standards. The benefits of engaging with this framework are multifaceted, offering competitive advantage and aligning with consumer expectations for sustainability.
In addition to regulations, incentive programs such as tax breaks or grants can persuade manufacturers to adopt cleaner technologies. Such incentives encourage a shift towards greener practices, benefiting both the environment and the economy.
Government Regulations and Incentives
Government regulations are often the cornerstone of a robust policy framework. These laws set the parameters within which businesses must operate. Key regulations may include emissions standards that limit the amount of carbon dioxide and other greenhouse gases a manufacturer can produce. Compliance is not just a legal necessity; it is also a public relations imperative in today’s environmentally-conscious market.
Moreover, government incentives can significantly influence the adoption of innovative technologies. For instance:
- Tax credits for renewable energy investments encourage manufacturers to transition from fossil fuels.
- Subsidies for adopting energy-efficient machinery lower the costs associated with such upgrades.
- Grants for research into sustainable practices foster innovation within the sector.
These incentives not only stimulate investment in cleaner technologies but also lead to a tangible reduction in carbon emissions.
International Standards and Agreements
International standards and agreements create a global framework for mitigating environmental impact. Entities such as the United Nations Framework Convention on Climate Change (UNFCCC) establish legally binding obligations on countries to limit their greenhouse gas emissions. Participation in these agreements compels nations to enforce domestic policies aligning with international sustainability goals, enhancing the credibility of local regulators.
Adopting internationally recognized standards, such as ISO 14001 for environmental management systems, provides a structured approach to managing environmental responsibilities. This standard offers manufacturers a guideline for enhancing their environmental performance through more efficient resource use and reduction of waste.
Furthermore, collaboration across borders facilitates knowledge sharing and the exchange of best practices. Industry leaders can reap significant advantages by embracing these global initiatives.
As nations reinforce their commitments to international agreements, companies can expect increased scrutiny regarding their carbon emissions. This added pressure can motivate them to invest in innovations that contribute to a more sustainable future.
"Sustainable manufacturing is not only a regulatory compliance issue; it is increasingly vital for companies seeking to align with global sustainability goals and respond to consumer demands for responsible production practices."
Through careful navigation of the policy landscape, manufacturers have a unique opportunity to enhance their sustainability efforts while achieving long-term economic benefits. The intersection between regulations, incentives, and international agreements represents a dynamic strategy for reducing the manufacturing carbon footprint.
The Role of Business in Carbon Footprint Mitigation
The role of business in reducing the carbon footprint is essential and multifaceted. Businesses operate at the intersection of consumer demand, production processes, and regulatory frameworks. Their position allows them to effect significant change in their strategies to address carbon emissions. As entities that generate substantial environmental impact, they can influence the sustainability landscape positively.
Corporate Social Responsibility
Corporate Social Responsibility, often abbreviated as CSR, signifies an organization’s commitment to ethical behavior and environmental stewardship. Companies are increasingly seen not just as profit-generating machines but as moral actors in society. This involves integrating social and environmental concerns in their operations and interactions with stakeholders.
Businesses that adopt proactive CSR strategies find benefits in several areas. Firstly, it enhances their brand image. Consumers are more likely to support companies that commit to sustainable practices. When firms engage in transparent socially-responsible behaviors, they build trust and foster a loyal customer base. Moreover, CSR efforts can lead to operational efficiencies, reducing waste and improving resource use.
The incorporation of CSR into business strategy also aligns with legal and regulatory pressures. Governments around the world are formulating stricter environmental regulations that demand accountability. Firms that take the initiative to implement sustainable practices often find themselves better prepared to comply and adapt to these regulations.
"CSR is not just a moral obligation but a strategic necessity for businesses in a rapidly changing world."
Setting Emission Reduction Targets
Setting emission reduction targets is crucial for businesses aiming to mitigate their carbon footprint. Targets provide a framework for action and accountability. By defining specific, measurable goals, a company can track its progress over time and make adjustments as needed.
Emission targets can vary widely. Some companies opt for science-based targets, aligning their sustainability goals with climate science to ensure they contribute effectively to global efforts in reducing greenhouse gases. Others may focus on incremental improvements, establishing short-term targets that build toward long-term commitments.
Additionally, public commitments to emission reduction can enhance a company's reputation and market position. Demonstrating transparency in setting and meeting these targets fosters video confidence among customers and investors. Furthermore, engaging employees in these initiatives can create a culture of sustainability within the organization, driving innovation and commitment.
In summary, businesses hold a pivotal role in carbon footprint mitigation through Corporate Social Responsibility and by setting robust emission reduction targets. Their actions affect not only their operational impact but also set precedents for their industry, showcasing leadership in the quest for a sustainable future.
Consumer Influence on Manufacturing Practices
Consumer behavior has increasingly become a significant factor in shaping manufacturing practices. As awareness of environmental issues grows, consumers are more inclined to support companies that demonstrate a commitment to sustainability. This section delves into the elements that illustrate this influence, particularly in relation to the demand for sustainable products and the role eco-labeling plays in guiding consumer choices.
Demand for Sustainable Products
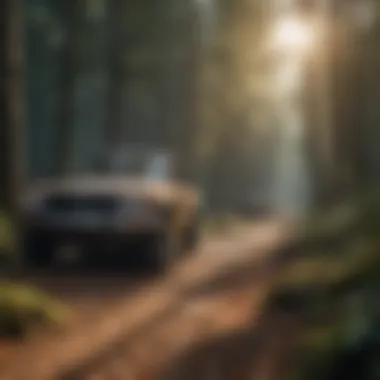
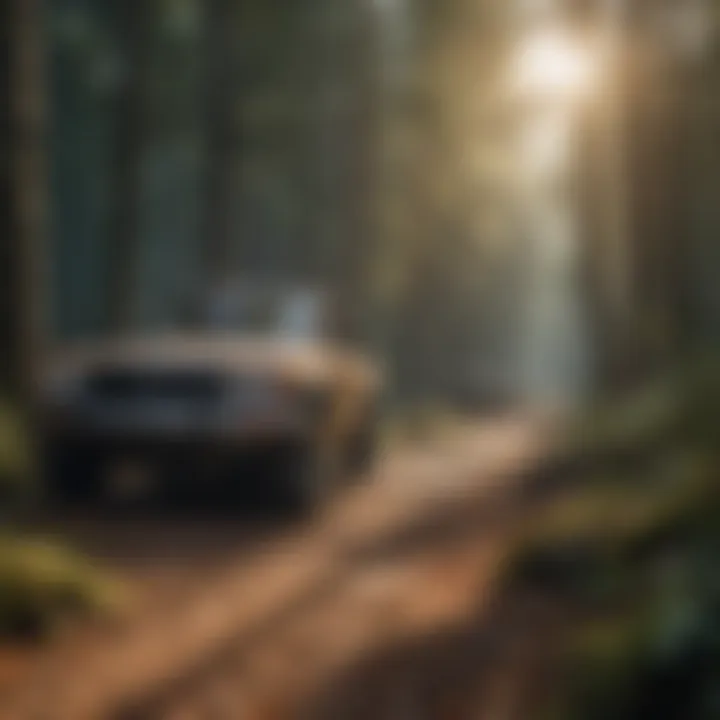
The demand for sustainable products reflects a fundamental shift in consumer expectations. Today’s consumer base is not only more knowledgeable but also more concerned with the implications of their purchases on the environment. Factors such as climate change, resource depletion, and pollution drive customers to seek products that minimize environmental impacts. This shift can prompt manufacturers to rethink their production processes and materials, often leading to innovations that lessen their carbon footprint.
As companies recognize the benefits of catering to this changing market, they implement practices such as:
- Sourcing eco-friendly materials: Manufacturers are inclined to use sustainable resources, such as recycled or responsibly sourced raw materials.
- Improved production methods: Investing in cleaner technologies and processes helps reduce waste and emissions, aligning with consumer demands for lower carbon footprints.
- Product longevity and recyclability: Consumers now prefer products designed for durability and recyclability, further encouraging manufacturers to reduce planned obsolescence.
In summary, the demand for sustainable products is driving manufacturers to innovate and adapt, which ultimately benefits the environment by reducing the overall carbon emissions associated with the manufacturing process.
Role of Eco-labeling
Eco-labeling is another crucial factor impacting consumer influence on manufacturing practices. These labels provide information about the environmental performance of products, helping consumers make informed decisions. Eco-labels can communicate essential details about a product's sustainability, such as carbon emissions, resource use, and lifecycle impact.
The effectiveness of eco-labeling lies in its ability to:
- Promote transparency: Labels offer clarity on what sustainability means for a product, educating consumers on their choices.
- Enhance brand loyalty: Companies that display eco-labels often enjoy increased consumer trust and loyalty, as buyers feel they are addressing environmental concerns through their purchasing habits.
- Encourage responsible manufacturing: The competitive pressure of obtaining eco-labels can drive manufacturers to adopt greener practices and improve their overall environmental performance.
In essence, eco-labeling empowers consumers by providing the information needed to support sustainable manufacturing. This shift in consumer behavior plays a pivotal role in shaping industry standards and practices, making sustainability a key consideration for manufacturers globally.
"Consumer choices can significantly impact the manufacturing landscape, as the collective demand for sustainable products encourages companies to innovate and prioritize environmental stewardship."
Together, the dynamics of consumer demand for sustainable products and the influence of eco-labeling underscore the importance of consumer engagement in the quest for reduced carbon footprints in manufacturing. As markets evolve, the responsibility lies with both consumers and manufacturers to foster practices that support sustainability.
Best Practices for Sustainable Manufacturing
Sustainable manufacturing represents not only an ethical consideration but also a strategic advantage in today’s increasingly competitive market. The importance of adopting best practices in sustainable manufacturing cannot be overstated. These practices help in reducing the carbon footprint of production processes while securing a competitive edge in an environmentally-conscious world.
Embracing sustainability is no longer optional for manufacturers; it is essential. Sustainable practices help companies to minimize waste, optimize resource usage, and ultimately lower costs. Furthermore, incorporating sustainable methodologies appeals to consumers, who are more inclined to choose environmentally responsible products. This trend affects both large and small manufacturers as the market shifts towards sustainability.
It is also critical to consider the long-term benefits realized through sustainability initiatives. By focusing on sustainable manufacturing practices, companies can build resilient supply chains that are adaptive to changing regulations and market demands. This adaptability can protect organizations from economic shifts, as firms that prioritize sustainability often lead industry trends.
Adoption of Circular Economy Principles
Circular economy principles play a pivotal role in sustainable manufacturing. This model emphasizes the importance of resource efficiency and waste reduction. Rather than the traditional linear approach of 'take, make, dispose', a circular economy promotes the continual use of resources through recycling, remanufacturing, and refurbishment.
The key elements of adopting circular economy principles in manufacturing include:
- Resource Recovery: Continually reclaiming materials keeps them in use and benefits the environment.
- Design for Longevity: Products need to be designed for durability and ease of repair.
- Recycling Programs: Establishing programs that encourage consumers to return used products for recycling further extends the life of materials.
Implementing circular economy principles can lead to significant reductions in carbon emissions. According to various studies, this can actually lower operational costs and foster innovation. Companies committed to sustainability also often see enhanced brand loyalty and improved public perception.
Collaborative Approaches in Supply Chain Management
Another crucial aspect of best practices for sustainable manufacturing is fostering collaborative approaches in supply chain management. Sustainable practices are most effective when they are applied across the entire supply chain, involving suppliers, manufacturers, and customers. Collaboration can facilitate sharing of information and strategies that enhance sustainability.
Key benefits of collaborative supply chain management include:
- Shared Resources: Partnering with suppliers allows for shared logistics and transportation, reducing overall emissions.
- Transparency: A transparent supply chain assists in identifying carbon hotspots and improving efficiencies.
- Innovation: Working together can spur creative solutions to sustainability challenges, as diverse perspectives offer unique insights.
By embracing collaboration, companies position themselves to create value not only for their own operations but also for their partners and stakeholders. This approach can drive systemic change throughout the industry, making substantial contributions toward making manufacturing more sustainable.
"Sustainability is not a sprint; it is a marathon. Collaboration is the key to reaching the finish line."
Future Trends in Manufacturing Carbon Footprint Reduction
Reducing the carbon footprint in manufacturing is crucial in the quest for environmental sustainability. As global awareness of climate change grows, manufacturers face increasing pressure to minimize emissions. Future trends in this area will shape how firms operate and innovate to comply with regulations and client expectations. By embracing these trends, the manufacturing sector can not only reduce its environmental impact but also position itself competitively within a transforming market.
Emerging Technologies
Technological advancements play a significant role in reducing carbon footprints. New developments, such as Internet of Things (IoT) devices, have enabled manufacturers to monitor energy use more closely. These technologies can optimize processes and identify inefficiencies, resulting in less energy consumption. For instance, smart sensors can reduce waste by detecting anomalies in production lines and thus decrease unnecessary emissions.
Additionally, innovations in materials science are leading to the creation of sustainable materials. Companies are now exploring bioplastics and recycled composites that generate fewer emissions during production. Moreover, 3D printing technology allows for on-demand manufacturing, potentially reducing transportation emissions and minimizing waste.
Here are some of the emerging technologies with potential to influence manufacturing carbon footprints:
- IoT and smart sensors for real-time data collection
- 3D printing that reduces material waste
- Advanced robotics improving efficiency and precision
- Sustainable material alternatives, such as bioplastics
Global Initiatives and Partnerships
International cooperation is essential in tackling emissions. Many global initiatives focus on collaborative efforts to reduce the manufacturing carbon footprint. Agreements like the Paris Climate Accord demonstrate a unifying framework for countries to commit to emission reductions. Many industries now align themselves with these goals, recognizing that sustainability can also lead to economic advantages.
Partnerships between companies and environmental organizations have become increasingly vital. These collaborations often lead to shared knowledge and best practices for reducing carbon emissions. Programs that encourage industries to participate in carbon offsetting or renewable energy projects are gaining traction. Such initiatives not only lower the carbon footprint but also foster a culture of sustainability within organizations.
To summarize:
- International agreements encourage commitment to emission reduction initiatives.
- Partnerships facilitate sharing of best practices and resources.
- Carbon offset programs drive investment towards sustainable projects.
"The transition towards sustainable manufacturing is not merely a trend; it is becoming an operational necessity for businesses worldwide."
By focusing on these future trends, the manufacturing sector can anticipate changes and adapt accordingly. This proactive approach can ultimately lead to a significant reduction in the carbon footprint, benefiting both the environment and the economy.
Culmination and the Path Forward
In closing, it is vital to recognize the far-reaching implications of the manufacturing carbon footprint. Every stage of the manufacturing process contributes to overall emissions. Understanding the depth of this issue is crucial because it influences not just environmental policies but also business strategies. Proper measurements and management can lead to significant reductions in carbon output, enhancing sustainability efforts regionally and globally.
This article highlights several key factors that can drive progress toward a reduced manufacturing carbon footprint. By advocating for energy efficiency improvements, embracing technological innovations, and adhering to sustainable practices, industries can significantly mitigate their environmental impacts. Moreover, the role of policy frameworks cannot be overlooked. Regulations can incentivize greener practices and foster a culture of accountability within businesses.
The path forward requires collaboration not only among manufacturers but also between consumers, policymakers, and technological innovators. Everyone has a stake in creating sustainable practices that minimize carbon emissions.
Recap of Key Points
- Understanding the manufacturing carbon footprint is crucial for sustainability.
- Key sources of emissions are present in every step of manufacturing:
- Technological advancements such as automation and carbon capture are pivotal.
- Businesses need to adopt Corporate Social Responsibility to proactively address their carbon footprint.
- Policies and regulations can drive change through incentives and standards.
- Raw Material Extraction
- Manufacturing Processes
- Transportation and Distribution
Implications for Future Manufacturing Practices
The future of manufacturing practices hinges on sustainable development. As consumers become more environmentally conscious, there will be a rising demand for products that align with these values. Adopting circular economy principles will be essential in meeting this demand while simultaneously reducing waste and emissions. Moreover, industry partnerships and collaboration will foster innovative approaches to sustainability, enabling more efficient supply chain management.