High Performance Plastics: Key Innovations and Applications
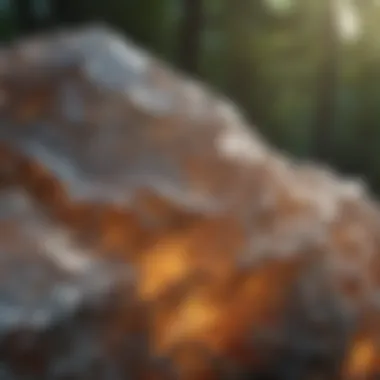
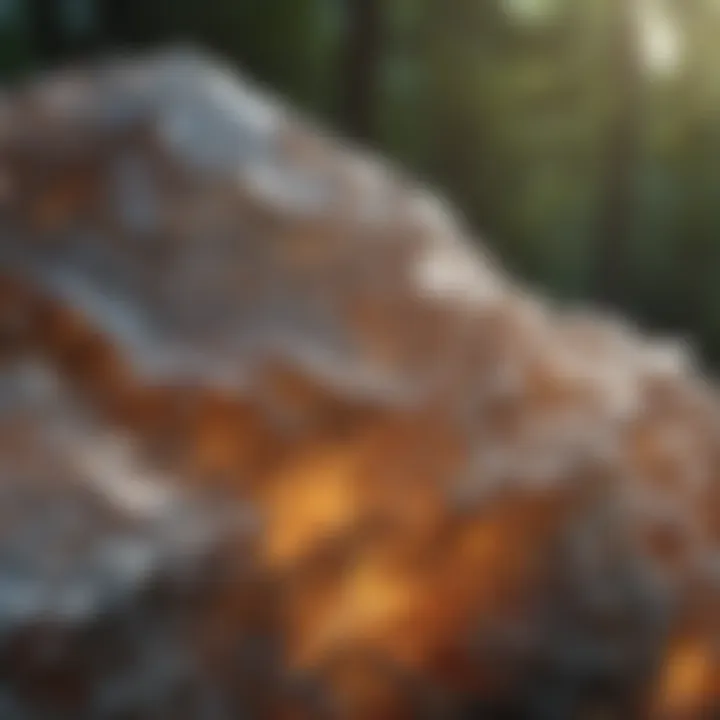
Intro
High performance plastics have become pivotal in various industries due to their outstanding mechanical and thermal properties. This article aims to provide a comprehensive insight into the intricate world of high performance plastics, such as PEEK, PTFE, and polyimides. We will explore their composition, distinctive features, applications, and the innovations driving their progress.
PLASTICS are traditionally seen as low-cost materials, but high performance variants significantly shift this paradigm. They are often designed for highly specialized applications where standard materials fail to meet required performance parameters. Understanding these materials is essential for professionals engaged in engineering, manufacturing, and sustainability initiatives.
Composition of High Performance Plastics
High performance plastics are engineered to withstand extreme environments. Their composition typically involves complex polymers that improve attributes such as heat resistance, chemical stability, and mechanical integrity. For example, PEEK (polyether ether ketone) exhibits excellent heat and chemical resistance, making it ideal for aerospace and medical applications.
PEEK
PEEK is known for its exceptional resistance to heat, chemicals, and wear. It can maintain mechanical performance in temperatures exceeding 300 degrees Celsius. Industries like aerospace and automotive leverage PEEK's properties for components that require durability under stress.
PTFE
Polytetrafluoroethylene, or PTFE, is another critical high performance plastic. Most notable for its non-stick characteristics, PTFE is thermally stable and chemically inert. It finds its applications in industries like food processing and electronics, where insulation and resistance to corrosive substances are paramount.
Polyimides
Polyimides are renowned for their versatility, often seen in applications that require superior thermal stability. They perform exceptionally well in electrical insulation applications and are vital in sectors like aerospace, electronics, and automotive.
Key Properties and Applications
Understanding the unique properties of high performance plastics informs their applications. These materials exhibit characteristics such as:
- Thermal Stability: They can endure high temperatures without degrading.
- Chemical Resistance: They resist corrosion and degradation from various chemicals.
- Mechanical Strength: High tensile strength contributes to applications where durability is essential.
Their applications span diverse fields:
- Aerospace: Used in components that must withstand extreme conditions.
- Medical Devices: Essential for creating biocompatible components.
- Electronics: Used in insulating materials due to their electrical resistance.
High performance plastics represent a vital intersection of material science and advanced engineering, driving innovation in critical sectors.
Innovations and Challenges in Development
The journey of high performance plastics involves relentless innovation. Factors such as sustainability and regulatory compliance push for advances in material formulation and processing techniques.
However, challenges remain. For instance, recycling high performance plastics is difficult due to their complex structures and the high thermal conditions required for processing. Addressing such challenges is pivotal for the future landscape of these materials.
Sustainability also plays a crucial role. The industry increasingly examines how to integrate sustainable practices without compromising performance. New methods, such as developing bio-based polymers, are being explored to alleviate environmental concerns.
In summary, high performance plastics are essential materials that are instrumental in various advanced applications. Understanding their composition, properties, and challenges provides invaluable insights for professionals in the field. Our exploration continues into the future potentials of these versatile materials.
Preface to High Performance Plastics
In today's rapidly evolving industrial landscape, high performance plastics hold a pivotal role. These advanced materials have garnered significant attention due to their exceptional properties. As technology continues to progress, the demand for materials that can withstand extreme conditions, exhibit light weight, and offer versatility grows. This section will highlight the essential elements that underpin the significance of high performance plastics.
Definition and Overview
High performance plastics can be defined as polymers specifically designed to operate under severe conditions, often exceeding the capabilities of standard plastics. These materials are characterized by their superior mechanical strength, thermal stability, and chemical resistance. Unlike conventional plastics, high performance variants maintain integrity and performance metrics in demanding environments, including high temperatures and aggressive chemical settings.
Their widespread applications include aerospace, automotive, electronics, and medical industries. Thus, understanding their unique properties is crucial for engineers and industry professionals who seek to leverage these materials in innovative ways. The integration of high performance plastics facilitates the development of cutting-edge solutions that improve efficiency and durability across various sectors.
Historical Context and Development
The evolution of high performance plastics dates back to the mid-20th century, when the first polymers with specialized properties were developed. Significant milestones include the introduction of materials like polyether ether ketone (PEEK) and polytetrafluoroethylene (PTFE). The quest to create materials that can endure high stress continues to drive research and development in this field.
The synthesis of these polymers often involves complex processes, including the tailoring of molecular structures to enhance performance characteristics. Over the years, advancements in material science have led to the emergence of newer and improved high performance plastics, which are more efficient and environmentally friendly. These developments are indicative of the industry's responsiveness to the escalating demand for sustainable and high-performing materials.
The growth of high performance plastics is not merely a trend; it's an evolution prompted by the needs of modern industries tackling more complex challenges than ever before.
Continued research will likely unveil further potential applications and innovative processing techniques, making high performance plastics integral to future technological advancements.
Key Characteristics of High Performance Plastics
High performance plastics (HPPs) possess unique properties that make them vital in various industrial applications. Understanding these characteristics allows engineers and professionals to select the optimal materials for specific needs. These plastics often outperform traditional materials, which enhances product durability, efficiency, and performance. The following sections will detail the key characteristics: thermal stability, chemical resistance, mechanical strength, and electrical insulation properties.
Thermal Stability
Thermal stability is a critical characteristic that defines how well a material can withstand high temperatures without degrading. High performance plastics such as Polyether Ether Ketone (PEEK) can endure temperatures exceeding 250°C (482°F). This is essential in industries such as aerospace and automotive, where components are often exposed to elevated thermal conditions. The ability to maintain structural integrity at high temperatures reduces the risk of failure, thus ensuring safety and longevity in applications.
Chemical Resistance
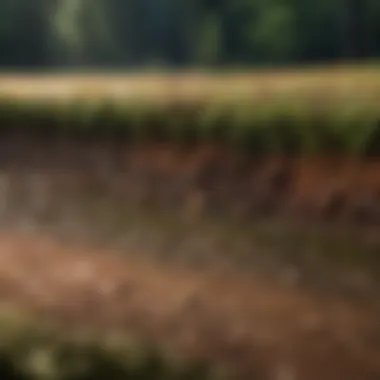
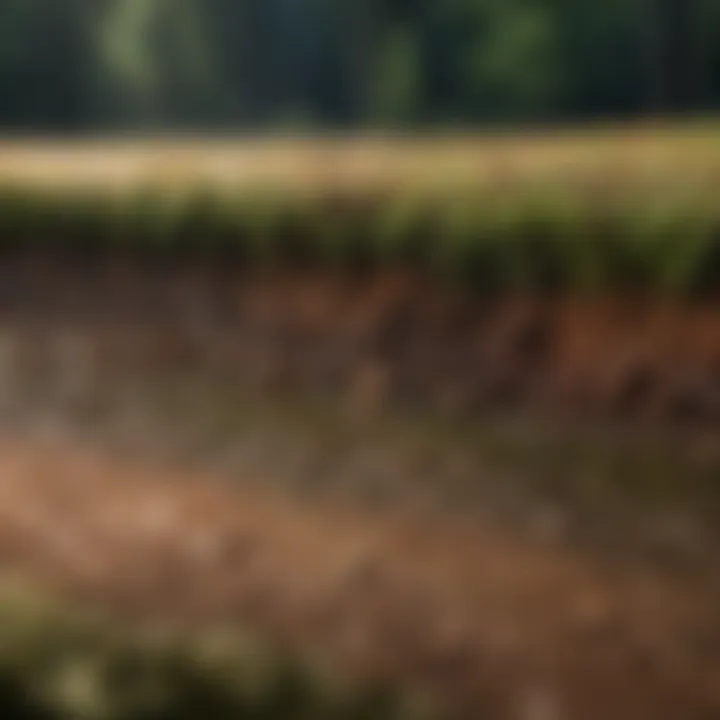
Chemical resistance is another defining feature of high performance plastics. These materials demonstrate remarkable resilience against acids, bases, solvents, and other corrosive substances. For instance, Polytetrafluoroethylene (PTFE) is highly regarded for its unique ability to resist the effects of aggressive chemistries. This characteristic is indispensable in industries such as chemical processing and pharmaceuticals, where materials are frequently subjected to harsh chemical environments. The long-term performance of these plastics minimizes the need for frequent replacements and repairs, leading to cost savings and increased efficiency.
Mechanical Strength
The mechanical strength of high performance plastics provides excellent load-bearing capabilities and resistance to deformation under stress. Polyimides, for example, offer high tensile strength and impact resistance. In applications requiring high strength-to-weight ratios, these plastics excel at replacing metals while providing weight advantages. This is particularly advantageous in the aerospace industry, where reducing weight contributes to improved fuel efficiency and overall performance.
Electrical Insulation Properties
Electrical insulation properties are vital for applications in electronics and electrical equipment. Liquid Crystal Polymers (LCP) demonstrate exceptional dielectric properties, making them suitable for use in circuits and components that require reliable electrical performance. The ability of high performance plastics to resist electrical breakdown ensures the safety and longevity of electronic devices, which is critical in advancing technology.
In summary, the key characteristics of high performance plastics—thermal stability, chemical resistance, mechanical strength, and electrical insulation properties—are fundamental to their widespread adoption in advanced applications.
The collective benefits of these properties underscore why high performance plastics are essential materials in today’s technological landscape. Understanding and leveraging these characteristics can enhance product design and performance across various sectors.
Types of High Performance Plastics
High performance plastics are integral in many industries, offering unique properties that suit specific engineering challenges. A clear understanding of the various types of high performance plastics enables professionals to make informed decisions regarding material selection based on factors such as application requirements, environmental conditions, and long-term durability. This section explores notable types of high performance plastics, each with its distinct characteristics, advantages, and use cases. Let's examine these materials in detail to appreciate their significance in modern engineering.
Polyether Ether Ketone (PEEK)
Polyether Ether Ketone, commonly abbreviated as PEEK, stands out due to its exceptional mechanical and thermal properties. This high performance plastic is known for its excellent chemical resistance and ability to retain strength at high temperatures. With a continuous service temperature of up to 260°C, PEEK is often chosen for applications that demand stability and durability in harsh environments.
PEEK is used extensively in aerospace, automotive, and medical industries. For instance, it's utilized in components such as electrical connectors, pumps, and seals, where other materials may fail. The material emphasizes not only high mechanical strength but also biocompatibility, making it suitable for medical implants.
Additionally, PEEK allows for various processing options, including injection molding and extrusion, further enhancing its versatility.
Polytetrafluoroethylene (PTFE)
Polytetrafluoroethylene, or PTFE, is widely recognized for its outstanding non-stick properties and exceptional resistance to heat and chemicals. Commonly known by the brand name Teflon, PTFE supports a range of applications where low friction and chemical inertness are critical. The operating temperature extends up to 260°C, while its dielectric properties make it suitable for electrical insulation.
In the realm of industrial applications, PTFE serves effectively in gaskets, seals, and lining materials, facilitating interactions with aggressive chemicals found in various petrochemical processes. Its low surface energy contributes to its hydrophobic characteristics, making it a key material in applications requiring water and dirt repellency.
Polyimides
Polyimides possess an array of beneficial thermal, mechanical, and electrical properties, making them suitable for high-temperature applications. Exhibiting stability at temperatures reaching 400°C, polyimides are often leveraged in aerospace and electronics. Their insulative capabilities are critical for applications in devices such as semiconductors.
The unique attribute of polyimides lies in their ability to maintain integrity under thermal and mechanical stress. For instance, they are often used in flexible printed circuit boards and gas turbine engines. Their high performance can be ascribed to a high degree of molecular orientation, which imparts a significant degree of stability and strength.
Liquid Crystal Polymers (LCP)
Liquid Crystal Polymers, or LCPs, stand out in terms of their remarkable strength-to-weight ratio and thermal stability. This category of high performance plastics can withstand high temperatures while maintaining their dimensional stability. LCPs are often used where mechanical strength and precision are critical.
A prime application area for LCPs is in the electronics industry, particularly in the manufacture of connectors and housing for electronic components. LCPs are also finding uses in automotive applications, especially in components that require high stiffness and low thermal expansion.
These polymers can be processed through conventional methods, but their unique flow characteristics allow for designs that can optimize mechanical properties even further, making them quite versatile in modern engineering solutions.
Understanding the specific properties and potential applications of each type of high performance plastic is crucial for driving innovation in the field.
As we observe the range of characteristics that these materials exhibit, it becomes clear that selecting the appropriate type of high performance plastic is pivotal for achieving desired performance outcomes in various settings. Each of these materials provides distinctive benefits, addressing unique challenges faced in advanced engineering.
Applications of High Performance Plastics
High performance plastics have transcended traditional roles in various industries. Their unique properties make them not just alternatives but often the materials of choice, particularly in demanding environments. Understanding these applications is essential for professionals across a range of fields, from engineering to health care. This section outlines the key industries where high performance plastics are pivotal, highlighting their benefits and considerations.
Aerospace Industry
In aerospace, weight reduction is vital for fuel efficiency and overall performance. High performance plastics such as Polyether Ether Ketone (PEEK) and Polytetrafluoroethylene (PTFE) are employed extensively. They provide substantial weight savings without compromising strength or durability. PEEK, for instance, resists extreme temperatures and chemicals, which are common in flight conditions. Additionally, these materials offer excellent fatigue resistance, ensuring long-term reliability in critical components.
Benefits include:
- Weight efficiency: Reduces fuel consumption and operational costs.
- Thermal resistance: Endures the harsh temperature variations of high-altitude flights.
- Chemical resistance: Protects against corrosion and degradation from fuels and hydraulic fluids.
Their use in applications like structural components, engine parts, and seals contributes significantly to enhanced safety and performance.
Automotive Industry
The automotive sector is increasingly turning to high performance plastics to improve efficiency and performance. Materials such as polyimides are integrated into systems that require thermal stability and lightweight characteristics. With rising regulations for fuel efficiency and sustainability, these plastics help manufacturers meet new standards.
Key advantages are:
- Durability: High performance plastics resist wear and tear, prolonging the lifespan of automotive parts.
- Temperature stability: Essential for engine components which operate under extreme conditions.
- Lightweight: Contributes to overall vehicle lightness, enhancing both performance and energy efficiency.
Common applications include fuel systems, electrical insulation, and structural components, where long-lasting durability is a prerequisite.
Electronics and Electrical Equipment
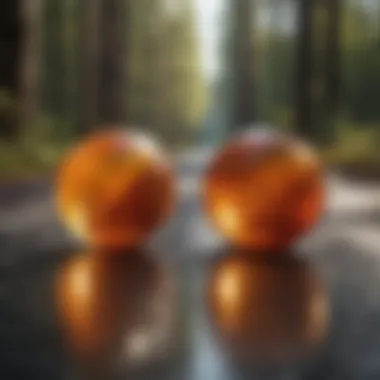
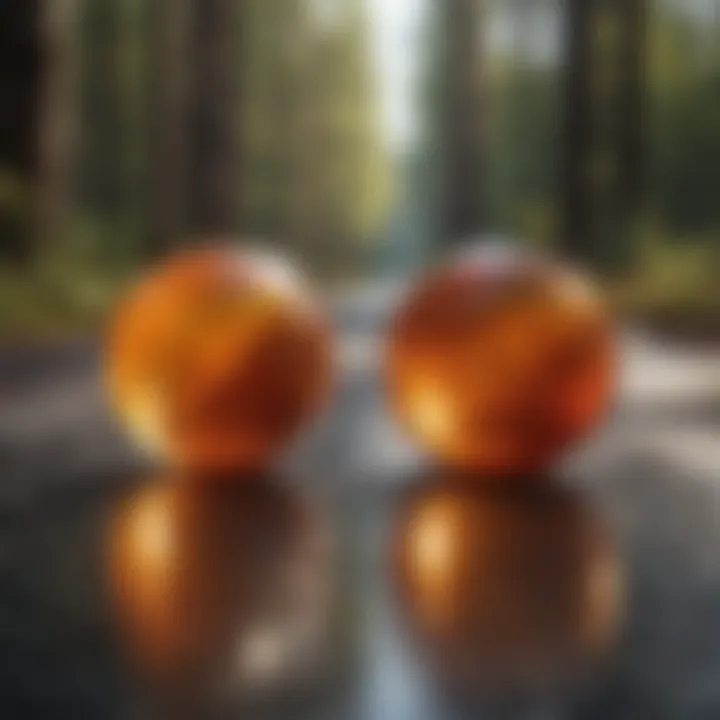
In the field of electronics, high performance plastics provide significant advantages due to their electrical insulation properties and thermal stability. Polymers like PTFE and polyimides are frequently used in circuit boards and connectors.
Highlights of their application in electronics consist of:
- Electrical insulation: Prevents short circuits and protects sensitive components from overheating.
- Thermal management: Maintains operational efficiency in devices exposed to heat.
- Chemical resistance: Safeguards electronics from corrosive substances.
These materials are critical for maintaining the reliability and safety of electronic devices in diverse applications.
Medical Applications
High performance plastics have become essential in the medical field, where biocompatibility and sterilization are critical. Polyimides and various fluoropolymers are used for surgical instruments, implants, and drug delivery systems. Their properties offer performance benefits that enhance patient safety and comfort.
Considerations in medical applications include:
- Biocompatibility: Reduced risk of adverse reactions when in contact with biological tissues.
- Sterilization capability: They can withstand the various sterilization processes needed for medical instruments.
- Durability: High performance under stress and temperature conditions, ensuring long-term function.
Applications significantly improve health outcomes and advance medical technologies.
"High performance plastics serve foundational roles across industries, underscoring their importance in modern engineering solutions."
Sustainability Considerations in High Performance Plastics
Sustainability considerations in high performance plastics are increasingly vital in today's global landscape. As awareness about environmental impacts rises, industries face pressure to develop materials that are not only efficient but also eco-friendly. High performance plastics play a significant role in this shift by providing alternatives that can reduce waste and promote responsible consumption. This section explores the critical elements within sustainability, focusing on recyclability, bio-based alternatives, and environmental impact assessments.
Recyclability and Reuse
High performance plastics often present unique challenges when it comes to recyclability. Due to their specialized properties, such as high thermal stability and chemical resistance, many of these plastics cannot be easily processed with conventional recycling methods. However, there are advancements in developing techniques that allow for the recycling of these materials. For instance, companies are investing in chemical recycling technologies that break down polymers into their basic building blocks.
Benefits of enhancing recyclability include:
- Reducing landfill waste: Approximately 30 million tons of plastic waste are generated annually in the United States alone. Improving recycling rates can mitigate this issue.
- Conserving resources: Recycling helps in recovering valuable raw materials, reducing the need for extraction and production of new ones.
- Lowering carbon footprint: Effective recycling processes save energy and decrease greenhouse gas emissions.
Bio-based Alternatives
In response to environmental concerns, the development of bio-based alternatives to traditional high performance plastics is gaining traction. These materials are derived from renewable sources, such as plants or biomass, which can help to minimize reliance on fossil fuels. Products like polylactic acid (PLA) show promise in specific applications where traditional high performance plastics are used.
Advantages of bio-based plastics include:
- Lower environmental impact: The production and disposal of bio-based materials typically generate fewer pollutants compared to conventional plastics.
- Biodegradability: Many of these alternatives offer the potential for composting and can decompose under specific conditions, reducing waste.
- Sustainable sourcing: Bio-based products can be produced with agricultural practices that encourage resource conservation.
Environmental Impact Assessment
Conducting an environmental impact assessment (EIA) is crucial in the development and implementation of high performance plastics. An EIA evaluates the potential effects of material production and usage on the environment and helps identify strategies for mitigating negative impacts. Key components of an effective EIA include:
- Life Cycle Assessment (LCA): A comprehensive approach that evaluates the environmental effects throughout a product's life cycle, from raw material sourcing to disposal.
- Regulatory Compliance: Ensuring that materials meet local and international environmental regulations is essential to sustainable practices.
- Stakeholder Engagement: Engaging with various stakeholders, including communities affected by plastic production, enhances transparency and accountability.
Processing Techniques for High Performance Plastics
Processing techniques play a crucial role in determining the usability and performance of high-performance plastics. These materials often exhibit superior properties, but the methods used to shape and manufacture them significantly influence their final characteristics, durability, and application potential. In this section, we will explore various processing techniques that enhance the performance of high-performance plastics, focusing on molding techniques, additive manufacturing, and blending and compounding methods. These methods not only affect the material properties but also address cost-efficiency and production challenges in a competitive market.
Molding Techniques
Molding techniques are essential for shaping high-performance plastics into usable forms. The most common methods include injection molding, compression molding, and extrusion. Each technique has its advantages, determined by factors such as the type of plastic, desired shape, and production volume.
- Injection Molding offers precision and repeatability, making it suitable for intricate designs. High temperatures are used to melt the plastic, which is then injected into a mold. This allows for complex geometries and tight tolerances, essential in industries such as aerospace and automotive.
- Compression Molding is another method that involves placing the plastic in a heated mold and applying pressure. Although it is generally suited for simple shapes, it allows for the production of larger parts more economically. This method is particularly useful for thermosetting plastics, which cure into solid forms when heat and pressure are applied.
- Extrusion continuously processes materials and is effective for creating long, continuous shapes like tubes or sheets. High performance plastics extruded in this way can be used for wire insulation or structural components in various applications.
In summary, the choice of molding technique can significantly impact the performance and applicability of high-performance plastics.
Additive Manufacturing
Additive manufacturing, commonly known as 3D printing, is transforming how high-performance plastics are utilized. This technique builds objects layer by layer, allowing for complex structures that traditional methods cannot easily achieve. The benefits of additive manufacturing include:
- Customization: It allows for personalization according to specific needs, an important factor in scientific and medical applications.
- Material Efficiency: This method reduces waste, as only the required amount of material is used, promoting sustainability.
- Rapid Prototyping: Products can be created and modified swiftly, accelerating the design process.
However, there are challenges too. The quality of printed parts can vary greatly depending on printer settings, materials used, and the specific application. Understanding the mechanical properties of high-performance plastics in the context of 3D printing is crucial for ensuring they meet the requisite performance standards in final applications.
Blending and Compounding Methods
Blending and compounding are vital to improving the properties of high-performance plastics. These methods involve mixing different polymers or adding fillers to enhance the performance characteristics of the base plastic. This process produces materials with tailored properties, suited for demanding applications. Some key points include:
- Enhancing Properties: Blending can improve strength, rigidity, or thermal stability. For instance, blending Polyether Ether Ketone (PEEK) with glass fibers can significantly enhance strength.
- Cost-Effectiveness: By compounding a more expensive polymer with a less expensive one, manufacturers can create materials that balance cost and performance effectively.
- Compatibility: Careful selection of base materials is necessary to ensure compatibility, as immiscible blends can lead to compromised material properties.
These processing methods are essential in developing high-performance plastics suited for specific functions and industries. Advanced knowledge and application of these techniques enable professionals to push the boundaries of what is achievable with these materials.
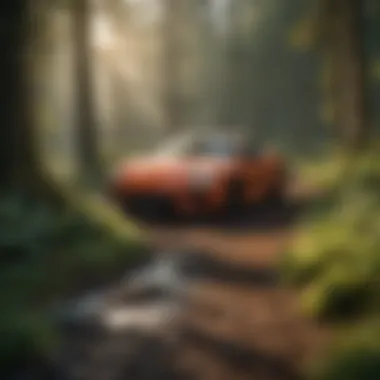
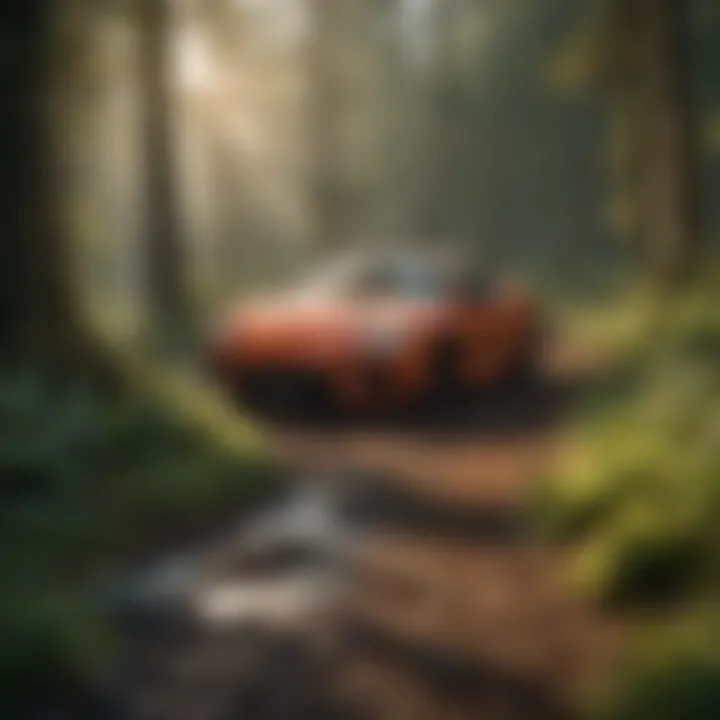
"Understanding the processing techniques for high performance plastics provides insights into how these materials can be effectively utilized to meet industry demands."
Challenges in the High Performance Plastics Sector
High performance plastics have a pivotal role in today's manufacturing and engineering landscapes. However, this sector also faces several distinctive challenges. Understanding these challenges is crucial for developers, engineers, and industry professionals. The complexities surrounding the production, performance, and supply chain significantly impact the overall viability and efficiency of high performance plastics.
Cost of Production
The cost of production for high performance plastics can be significant. These materials often require specialized processing techniques and high-quality raw materials.
- Raw Material Sourcing: Sourcing top-grade polymers tends to be expensive. This factor directly affects the pricing of final products.
- Processing Techniques: Techniques such as molding and compounding are more complex than traditional plastics. This complexity adds to the overall cost.
- Investment and Equipment: The machinery and technology necessary for producing high performance plastics are usually costly. Investing in such equipment requires considerable financial resources.
These factors combined can make high performance plastics less appealing compared to more common materials. Thus, ongoing research into reducing production costs is essential for the sustainability of the sector.
Performance Limitations
While high performance plastics offer excellent properties in many respects, there are still performance limitations that need to be addressed. Some key points include:
- Temperature Thresholds: Despite improved thermal stability, some polymers still exhibit limitations under extreme conditions.
- Mechanical Fatigue: Certain high performance plastics may not withstand continuous mechanical stress over long periods. This can lead to premature failure in critical applications.
- Environmental Performance: Not all high performance plastics perform equally well in various environmental settings. Some may degrade when exposed to specific chemicals or radiation.
Addressing these limitations is vital for expanding the applications of high performance plastics. Researchers are working to develop new formulations that can withstand extreme conditions without compromising performance.
Supply Chain Issues
The supply chain for high performance plastics is often intricate and susceptible to disruptions. Several concerns pose difficulties in this area:
- Raw Material Availability: The specialized nature of materials can lead to scarcity. If key resources become limited, the entire production cycle can be compromised.
- Manufacturing Bottlenecks: Sophisticated production processes can result in bottlenecks within manufacturing. When a specific step is delayed, it affects overall delivery times.
- Logistics and Distribution: Dependence on specialized logistics can complicate distribution networks. Efficient transport of high-value materials is essential to prevent delays and ensure timely deliveries.
These supply chain issues can hinder the growth potential of high performance plastics. Therefore, collaboration between manufacturers, suppliers, and researchers is imperative to fortify the supply chain against future challenges.
"Navigating the challenges of high performance plastics is essential for tapping into their vast potential within multiple industries."
Future Trends in High Performance Plastics
The landscape of high performance plastics is rapidly evolving. As industries increase their reliance on advanced materials, understanding the future trends is crucial. These trends not only shape the future of manufacturing but also drive innovation that can enhance product performance and sustainability.
Innovations in Material Science
Recent advances in material science are pushing the boundaries of what high performance plastics can achieve. Researchers are exploring new composites that combine superior mechanical properties with reduced weight. For instance, thermoplastic composites are being investigated for applications in aerospace and automotive sectors, where reducing weight without compromising strength is essential.
Another significant area is the development of bio-based high performance plastics. These materials, derived from renewable sources, promise to reduce dependence on fossil fuels. Innovations in polymer chemistry are enabling the creation of materials that not only perform at par with traditional counterparts but are also environmentally friendly.
"The shift toward sustainable materials is not just a trend; it is a necessity for future growth in various industries."
Integration of Smart Technologies
The integration of smart technologies into high performance plastics is emerging as a significant trend. Smart polymers are materials that can respond dynamically to environmental stimuli, such as temperature or chemical exposure. This responsiveness can enhance safety and efficiency in critical applications, especially in medical devices and automotive systems.
Moreover, the incorporation of sensors into high performance plastics allows for real-time monitoring of conditions and performance. Such technologies can inform predictive maintenance, minimizing risks and enhancing the longevity of applications.
Market Projections and Growth Areas
Market projections for high performance plastics are optimistic, indicating robust growth driven by diverse sectors. The aerospace and automotive industries are expected to be the largest consumers of high performance plastics due to their demand for lightweight and durable materials. According to current research, the global high performance plastics market is expected to reach significant value in the next few years, fueled by increasing investments in advanced manufacturing technologies.
Growth areas also include electronics, where the push for miniaturization and enhanced performance creates demand for innovative insulating materials. The medical sector is also expanding the use of high performance plastics, particularly in prosthetics and implants.
In summary, the future trends in high performance plastics highlight a commitment to innovation. The intersection of materials science, smart technologies, and vibrant market growth creates an exciting horizon for professionals and researchers alike.
Closure and Implications
The exploration of high performance plastics highlights their critical role in various industrial applications. This conclusion synthesizes the insights gained throughout the article, emphasizing the significance of these materials in modern engineering and manufacturing processes. High performance plastics, such as PEEK and PTFE, offer advanced properties that enhance functionality and efficiency across diverse sectors. Understanding these implications is vital for professionals who aim to implement these materials in innovative ways.
Key elements from the discussion include:
- Innovative Applications: The versatility of high performance plastics allows their use in the aerospace, automotive, and medical fields. Each application showcases the performance characteristics that lead to improved outcomes and solutions in challenging environments.
- Sustainability Considerations: The move towards recyclable and bio-based materials demonstrates an increasing awareness of environmental impacts. Ensuring sustainability in the production and disposal of these plastics is becoming a necessary consideration for manufacturers and end-users alike.
- Future Trends: Innovations in material science and the integration of smart technologies are shaping the future of high performance plastics. These developments promise to increase their applicability and efficiency in forthcoming applications.
In summary, as industries continue to advance and develop, the importance of high performance plastics will only grow. Their unique properties contribute to significant advancements in technology and environmental consciousness.
Summary of Key Points
Throughout this article, several core themes emerge regarding high performance plastics:
- Definition and Overview: High performance plastics are defined by their exceptional thermal, chemical, and mechanical properties.
- Characteristics: Key characteristics include thermal stability, chemical resistance, and electrical insulation, making them suitable for demanding situations.
- Types: Various types of high performance plastics, such as polyether ether ketone, polytetrafluoroethylene, and polyimides, serve specialized applications due to their unique attributes.
- Applications: Their applications span across multiple industries, including aerospace, automotive, and medical, reflecting their versatility.
- Sustainability: There is a growing need for recyclable solutions and alternative materials that lessen environmental impact.
- Challenges: Cost and performance limitations create difficulties in widespread use and could affect future innovations.
- Future Trends: Continuous advancements in material science will likely lead to new high performance plastics and applications.
Final Thoughts on High Performance Plastics
In closing, high performance plastics stand poised to revolutionize numerous industries due to their unmatched qualities. As professionals, it is essential to remain informed about industry developments and innovations. The capacity of these materials to offer solutions to critical challenges drives an ongoing interest and investigation into their properties and developments.
The breadth of applications and future innovations in high performance plastics reveal a material landscape rich with potential, shaping the future of technology and engineering.
Keeping these factors in mind not only enhances comprehension but also promotes thoughtful decision-making regarding material selection and implementation in various fields.