Equipment Cost Calculator for Forestry Management
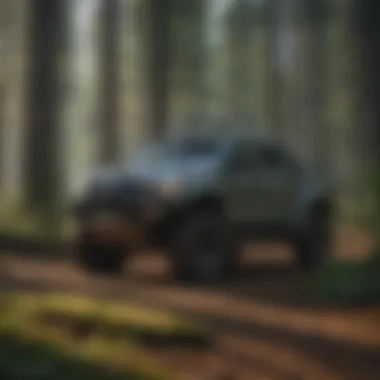
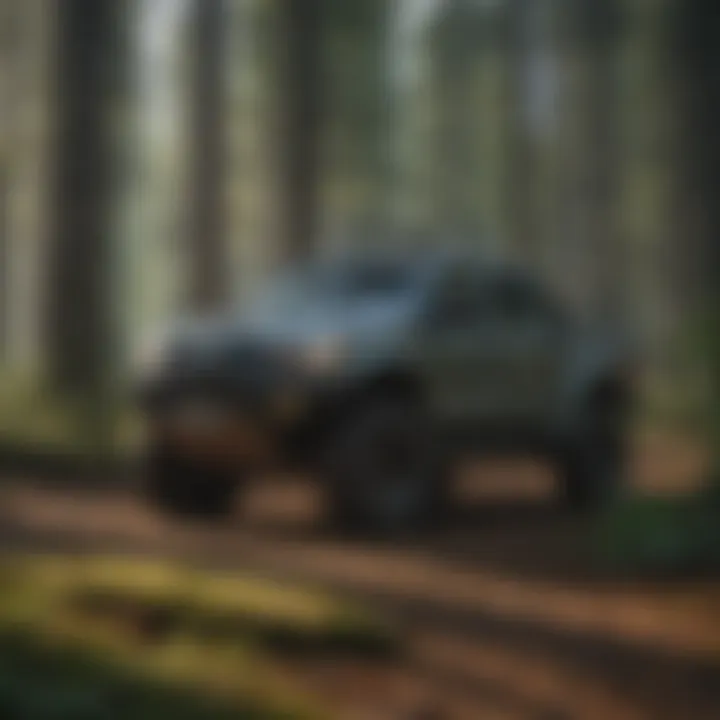
Intro
In the evolving field of forestry management, understanding the intricacies of equipment costs is paramount. A well-crafted equipment cost calculator spreadsheet serves as an invaluable tool for forestry professionals and enthusiasts alike. This guide will explore the significance of accurately assessing equipment costs, delve into the various components that influence these calculations, and discuss practical applications that aid informed financial decisions. By optimizing resource management, individuals can foster sustainability and effectively manage their woodland stewardship practices.
Understanding Forestry Practices
Modern forestry encompasses a range of practices aimed at ensuring the health and profitability of forest ecosystems. The complexities of these practices necessitate a keen understanding of the costs associated with various equipment used in the field.
Types of Forestry Practices
Forestry practices can be categorized into different types, each with specific methodologies and objectives:
- Sustainable Forestry: This approach emphasizes maintaining forest health while meeting economic needs. Strategies include selective logging and replanting.
- Commercial Forestry: Focuses on timber production for profit, often involving large-scale operations.
- Agroforestry: Integrates agriculture and forestry, promoting biodiversity and achieving higher productivity.
- Conservation Forestry: Aims to protect ecosystems, focusing on habitat preservation and biodiversity rather than solely on timber production.
Understanding these practices allows for a more thorough analysis of the financial implications tied to equipment use.
Historical Context
The evolution of forestry practices has been largely shaped by societal needs and technological advancements. Historically, forestry was often marked by a lack of understanding regarding sustainabilityโleading to practices that depleted resources.
With gradual recognition of the ecological impacts, current practices are more aligned with sustainable management principles. This historical context is essential for forestry professionals to appreciate the importance of sound financial practices, illustrated through effective cost analysis techniques.
Principles of Woodland Stewardship
Woodland stewardship involves responsible management of forested resources to ensure their sustainability for future generations. This principle is grounded in methods that balance ecological health with economic viability.
Conservation Techniques
Utilizing various conservation techniques is crucial for maintaining healthy forest ecosystems. These techniques may include:
- Controlled Burns: Used to reduce excess brush and improve habitat health.
- Reforestation: Involves planting trees in deforested areas to restore ecosystem balance.
- Invasive Species Management: Focusing on removing non-native species that threaten biodiversity.
Such techniques underscore the importance of careful planning and resource allocation, thus directly linking to equipment costs.
Managing Forest Resources
Effective resource management relies on precise calculations of costs associated with equipment use. Decisions made at this level can have lasting effects on both the economic and ecological aspects of forest management. Understanding how to efficiently allocate funds for equipment can significantly impact forestry operations, emphasizing the need for a robust cost calculator.
Sustainable Forest Management
Sustainable forest management integrates ecological, economic, and social dimensions to enhance overall forest health. Recognizing and implementing sustainability measures significantly enhances financial decision-making processes.
Certification Standards
Various certification standards exist, such as the Forest Stewardship Council (FSC) and the Programme for the Endorsement of Forest Certification (PEFC). These certifications assure buyers that products come from responsibly managed forests, which demand higher pricing.
Economic Benefits of Sustainability
Adopting sustainable practices yields long-term economic benefits, including:
- Increased Market Access: Certified products often access premium markets.
- Value-Added Products: Sustainable practices can lead to diversification and higher profitability.
- Cost Savings: Reducing waste and improving efficiency lead to lower operational costs.
Sustainable forest management is not merely an ethical imperative but a strategic advantage in todayโs marketplace.
Preface to Equipment Cost Calculation
Accurate equipment cost calculation is crucial in forestry management. This process helps in understanding not just the expenditure but also the long-term financial sustainability of forestry operations. By calculating costs accurately, professionals make informed decisions that can impact the entire lifecycle of forestry projects. This includes budgeting, purchasing decisions, and resource allocation.
The forest industry faces unique challenges that necessitate precise cost management. Equipment costs can significantly influence overall project budgets. They include direct expenses like purchase price and indirect costs such as maintenance and depreciation. By recognizing and calculating all related costs, forest managers can develop strategies that enhance operational efficiency and ensure better stewardship of resources.
Additionally, understanding equipment costs promotes transparency in financial reporting. Stakeholders, from investors to regulatory bodies, require clarity regarding financial dealings. Accurate cost assessment aids in demonstrating value for money, fostering trust, and securing funding for future projects.
Importance of Accurate Cost Assessment
Accurate cost assessment offers several key benefits. First, it allows forestry professionals to establish a clear financial picture. Knowing the costs of equipment involved helps in determining the feasibility of projects. Second, by having solid data, managers can make realistic forecasts and set achievable budgets. This minimizes the risk of overruns that could jeopardize project viability.
Moreover, accurate assessments enhance decision-making. When all costs are well understood, it becomes easier to compare options. For example, should one invest in high-end equipment now or opt for cheaper alternatives? These decisions impact operational efficiency and can alter the financial landscape of an undertaking.
Accurate cost assessments are not merely numbers; they represent informed choices that shape forestry initiatives.
Finally, comprehensive cost data facilitate performance evaluation. By comparing actual expenditure against projections, organizations can learn from past experiences, adjusting future budgeting approaches accordingly. This adaptability is vital in the dynamic forestry sector.
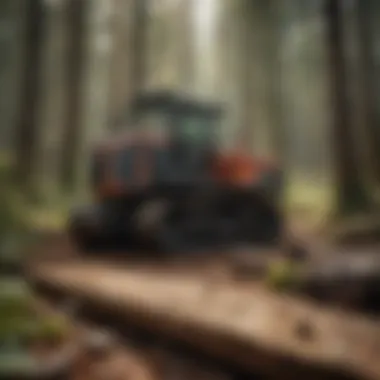
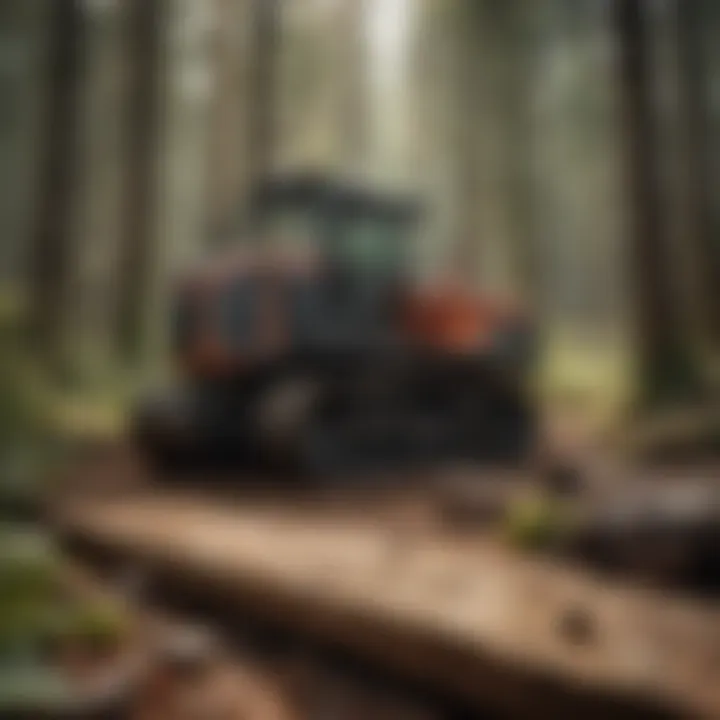
Overview of Equipment Cost Calculation
Equipment cost calculation encompasses a range of factors, making it a complex but essential component of forestry management. At its core, it involves identifying all relevant costs associated with the use of machinery and tools. The process starts with identifying fixed costs, such as the purchase price of equipment, and continues through to variable costs like fuel, maintenance, and operation.
In addition, indirect costs, which may not be immediately apparent, must also be factored in. These can include administrative expenses, insurance, and depreciation. Each of these components impacts the bottom line in subtle but significant ways. Therefore, it is important to implement a holistic approach to cost calculation that does not overlook these elements.
By leveraging tools like an equipment cost calculator spreadsheet, forestry managers can systematically lay out these costs. A well-structured spreadsheet can provide clarity in calculations. It allows variations to be applied, enabling scenario planning for future projects. This foresight is particularly valuable given the uncertainties that often accompany forestry management.
Understanding Equipment Costs
Understanding equipment costs is a critical part of forestry management. Knowing the costs associated with various equipment allows forestry professionals to make informed financial choices. This knowledge contributes to budget planning and allocates resources efficiently. Accurate cost assessment helps in optimizing operational practices, leading to sustainable growth within the industry.
Types of Equipment Costs
Fixed Costs
Fixed costs are expenses that do not change with the level of output. They include items like insurance, equipment leasing, and certain administrative expenses. These costs are predictable and stable, making it easier to estimate overall project costs. This predictability is a crucial aspect for managing long-term forestry projects. A key characteristic of fixed costs is their consistency throughout the equipment's usable life.
While fixed costs are generally beneficial for planning, they can present challenges if changes in operation occur. For instance, an increase in operational scale may not proportionately affect fixed costs, creating a disparity in the cost per unit of output.
Variable Costs
Variable costs fluctuate based on the level of activity in forestry operations. These might include fuel, repairs, and labor, all of which increase with heightened equipment usage. A notable aspect of variable costs is their direct correlation with operational intensity. This characteristic allows forestry managers to control expenses more effectively by adjusting the scale of operations according to demand.
One unique feature of variable costs is their potential for unpredictability, which can impact budgeting efforts significantly. Understanding these costs is essential for agile decision-making. However, while they offer flexibility, they can also complicate long-term financial forecasting.
Indirect Costs
Indirect costs, also known as overhead, refer to expenses that are not directly tied to any single piece of equipment or project. Items like administrative costs and utilities fall under this category. The fundamental aspect of indirect costs is their shared nature, affecting multiple projects at once.
These costs are often harder to allocate accurately, posing challenges in detailed financial analysis. However, their consideration is crucial for creating a comprehensive understanding of overall project costs. Managing indirect costs effectively can contribute significantly to enhanced profitability, although it can prove complex to track and allocate correctly.
Factors Influencing Equipment Costs
Market Prices
Market prices significantly affect equipment costs in the forestry sector. Fluctuating prices can arise from supply chain disruptions or changes in demand for specific types of machinery. The volatility of market prices is a critical factor that requires regular monitoring. As such, staying informed about industry trends is necessary for making strategic purchasing decisions.
A unique feature of market prices is their impact on both immediate and long-term budgeting. Properly anticipating market shifts can lead to substantial savings. However, sudden price spikes could adversely affect project feasibility, necessitating alertness and adaptability in financial planning.
Maintenance Expenses
Maintenance expenses are ongoing costs incurred to keep equipment operational. These can include repairs, inspections, and routine maintenance. The significance of maintenance expenses in forestry management lies in their potential to prolong the life of equipment, thus impacting overall costs. A key characteristic is that they can often be anticipated and planned for; however, unexpected breakdowns can lead to sudden costs.
Consistent maintenance practices can reduce long-term costs, enhancing operational efficiency. But, if neglected, maintenance expenses can exceed initial expectations. Therefore, monitoring and planning for these costs is crucial.
Depreciation Rates
Depreciation rates reflect the reduction in value of equipment over time. Recognizing these rates is essential for making informed financial decisions regarding equipment purchase or leasing. A critical aspect of depreciation is its effect on asset valuation, affecting both balance sheets and tax considerations.
The unique feature of depreciation is that it can vary significantly based on the type of machinery, usage level, and market conditions. Accurate depreciation accounting helps in determining the right time to replace equipment, ensuring that finances remain stable. However, misestimating depreciation can lead to significant financial discrepancies, affecting forecasting and operational budgets.
Components of an Equipment Cost Calculator Spreadsheet
In the arena of forestry management, the effective allocation of resources is critical. The components of an equipment cost calculator spreadsheet form the backbone of successful financial assessment. Each element plays a unique role in ensuring the tool is both comprehensive and user-friendly. Understanding these components helps users make informed decisions, thereby enhancing both operational efficiency and financial transparency.
Essential Spreadsheet Structure
Input Fields
Input fields are the first point of interaction within the spreadsheet. They gather essential data from the user, such as equipment type, purchase cost, and operational hours. This feature is fundamental as it directly impacts the accuracy of the outputs generated by the spreadsheet. A well-designed input field is simple yet comprehensive; it allows for the entry of various information critical for cost assessment. The key characteristic of good input fields is clarity. Users must easily understand what data is required.
The unique aspect of input fields is their adaptability. They can be modified to fit specific forestry needs. However, attention is required to avoid ambiguity or incorrect entries, which can skew the results.
Calculation Formulas
Calculation formulas are vital for processing the data entered in the input fields. These formulas perform the computations that determine overall costs, depreciation, and other metrics crucial for effective management. Their importance cannot be overstated, as they directly link raw data to actionable insights. A key feature is their ability to automate complex math, eliminating manual errors.
The unique aspect of calculation formulas lies in their accuracy. Benchmarked against industry standards, they offer reliable outputs that aid in financial planning. Nevertheless, it's essential to maintain the formulas for any updates in market conditions or operational changes.
Output Sections
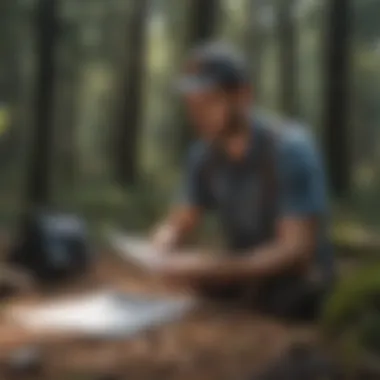
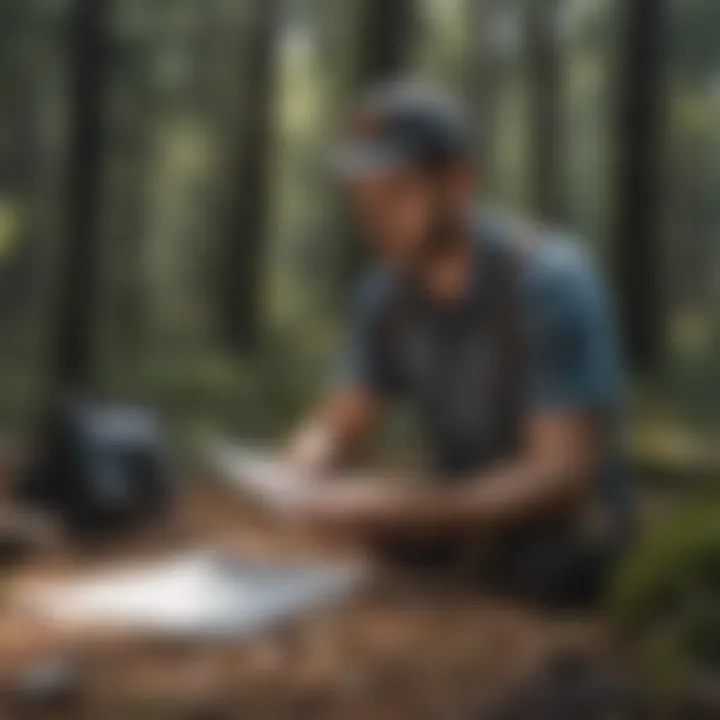
Output sections present the results derived from the calculations, summarizing costs and insights in an easy-to-understand format. This component serves as the final product of the data-processing phase, highlighting key figures such as total costs and estimated profitability. A significant feature is that these sections often include visual elements, like charts or tables, that enhance comprehension.
Their unique advantage is clarity. Clear output sections facilitate better interpretative discussions among team members or stakeholders. However, an overly complex output can lead to confusion and misinterpretations that impact decision-making.
Common Formulas Used
Total Cost Calculation
Total cost calculation is essential as it provides a holistic view of all expenditures related to equipment. This formula aggregates fixed, variable, and indirect costs to present a clear financial picture. Its key characteristic is the comprehensive nature of this calculation, making it invaluable for budgeting and financial forecasting. The unique benefit is its ability to highlight areas where costs can be optimized. However, precision in data entry is critical; inaccuracies can lead to flawed assessments.
Depreciation Calculation
Depreciation calculation accounts for the decline in value of equipment over time, enabling more accurate financial assessment. This formula is particularly crucial in forestry, where equipment can be a significant investment. The key characteristic of depreciation calculation is its time-based nature, allowing for long-term financial strategies. A unique benefit is the ability to incorporate various methods of depreciation, offering flexibility. However, it can become complicated if assumptions about usage or lifespan are inaccurate.
Break-even Analysis
Break-even analysis aids in determining when a project or investment will become profitable. This formula evaluates the relationship between costs and revenue. A key feature is its simplicity; it provides straightforward insights into profit margins. This analysis is advantageous for making rapid financial decisions in forestry projects. However, reliance on estimated values can lead to misleading conclusions about profitability timelines.
In summary, the components of an equipment cost calculator spreadsheet are crucial for forestry management. They ensure the accuracy and clarity of financial assessments, ultimately aiding in resource optimization and sustainable practices.
Steps to Create an Effective Equipment Cost Calculator
Creating an effective equipment cost calculator requires careful planning and a systematic approach. This process is crucial for forestry management as it leads to informed financial decisions. A well-structured calculator not only calculates costs effectively but also enables better budgeting and resource allocation. It highlights expenses involved in different activities, ensuring that special attention is given where necessary.
Defining Your Equipment List
The first step in creating your equipment cost calculator is to define your equipment list. This list should be comprehensive and updated regularly. Begin by categorizing equipment based on usage. For instance, you may have categories for felling, skidding, and processing. Each of these categories may include various tools or machines such as:
- Chainsaws for tree cutting.
- Forwarders for transporting logs.
- Chippers for processing wood waste.
In addition, make sure to include all relevant equipment within your current inventory. Understanding what equipment you possess allows for better estimation of costs associated with operation and maintenance. Consider also any equipment that may need to be purchased in the future. This foresight can help in planning for capital expenditures.
Gathering Relevant Cost Data
Once your equipment list is defined, the next critical step is gathering relevant cost data. Accurate data is necessary for an effective cost calculator. Begin by collecting information on the acquisition costs of each piece of equipment. This includes purchase price, shipping, and installation costs. However, the cost does not end there. You must also take into account:
- Operating costs: This includes fuel, oil, and other consumables.
- Maintenance expenses: These can vary over time and should include regular servicing and unexpected repairs.
- Insurance costs: Protecting equipment can be an essential part of budgeting.
- Depreciation rates: Understanding how equipment value decreases over time is crucial for your financial forecasting.
Consider consulting external sources for market prices. This can provide insights into whether your estimated costs align with industry standards. Data quality plays a vital role in your calculator. There should be a consistent system for updating values to reflect current market conditions.
Gathering data efficiently will enhance the overall reliability of your calculator. The objective should be to create a tool that not only serves todayโs needs but also adapts to changes in the market, thereby remaining relevant and effective over time.
Practical Applications of the Equipment Cost Calculator
The Equipment Cost Calculator Spreadsheet serves as more than just a financial tool; it embodies a bridge between project planning and financial analysis in forestry management. The practical applications of this calculator enable forest managers, landowners, and investors to engage in rigorous budgeting and facilitate informed decision-making. Cultivating a solid grasp of these applications will significantly enhance the overarching effectiveness of forestry operations.
Budgeting for Forestry Projects
Budgeting is the backbone of any successful forestry project. An accurate budget is critical for ensuring that financial resources are allocated efficiently, enabling the fulfillment of project objectives. With the use of the equipment cost calculator, managers can identify all possible equipment-related costs, which include but are not limited to:
- Acquisition Costs: The upfront investment required to purchase or lease equipment.
- Operational Costs: This encompasses fuel, maintenance, and labor charges.
- Depreciation: Understanding how equipment loses value over time aids in long-term financial planning.
By inputting these variables into the calculator, forestry managers can create a detailed financial forecast. This approach empowers them to evaluate whether a project is viable or requires adjustments before implementation. Most importantly, it highlights areas of potential overspending that can be adjusted before costly commitments are made.
Long-term Investment Planning
Long-term investment planning is essential for sustainable forestry management. Tools like an equipment cost calculator provide vital insights that guide investment strategies. By estimating future costs accurately, professionals can make informed decisions about:
- Equipment Upgrades: Knowing when to replace or upgrade equipment based on cost analysis improves efficiency and productivity.
- Resource Allocation: Proper foresight allows for better allocation of resources, minimizing waste and maximizing returns.
- Financial Projections: Evaluating potential returns on investment (ROI) from using specific equipment aids in assessing long-term gains versus expenditure.
Ultimately, forestry professionals can utilize these insights for strategic growth and expansion. They can better assess the financial health of their operations and optimize their asset utilization. As conditions in markets evolve, being well-equipped with data allows for proactive adaptations in strategy.
Utilizing an equipment cost calculator leads to a more informed approach to budgeting and planning, reducing risk and enhancing profitability.
Benefits of Using an Equipment Cost Calculator Spreadsheet
Using an equipment cost calculator spreadsheet can be transformative for forestry management. Accurate cost calculations are essential in forestry, where investments in equipment play a crucial role in operational efficiency and resource preservation. This section will discuss how a dedicated spreadsheet can not only enhance financial understanding but also improve decision-making processes in the forestry sector.
Enhanced Financial Understanding
An equipment cost calculator spreadsheet provides a clear, structured view of all associated costs. This clarity helps forestry professionals grasp the full scope of financial requirements for their operations. By breaking down expenses into categories such as fixed costs, variable costs, and indirect costs, users can see where their money is going.
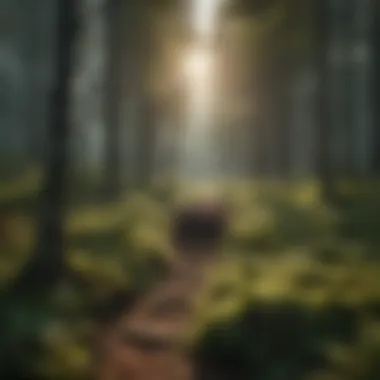
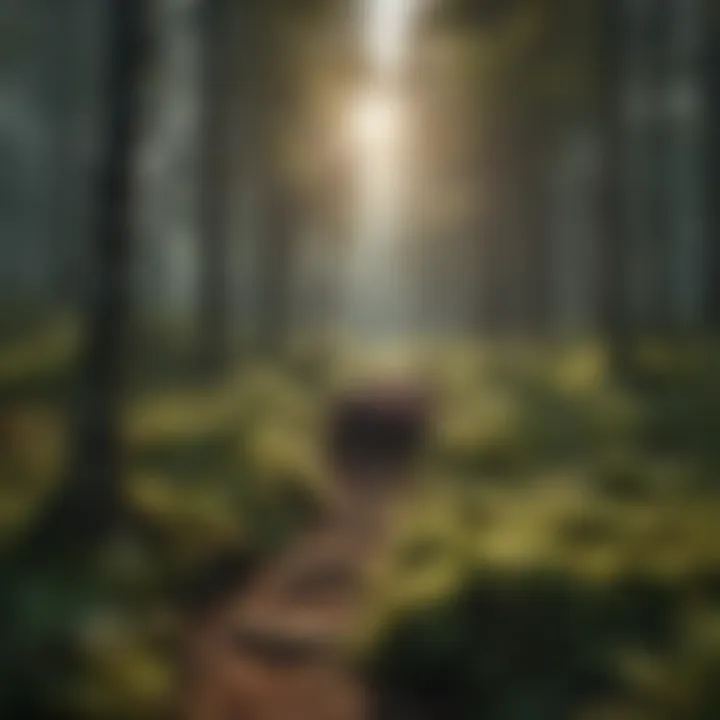
Tracking expenses meticulously enables managers to forecast budgets more accurately. With historical data, they can identify patterns in costs, which aids in planning future projects. Additionally, the inclusion of depreciation rates facilitates a deeper understanding of how equipment loses value over time, impacting overall financial planning. Knowing these figures supports better allocation of resources.
Furthermore, when engaging in project proposals or seeking funding, showcasing comprehensive cost analysis builds credibility. Potential investors or stakeholders appreciate well-prepared financial insights that demonstrate the viability of forestry projects.
Improved Decision-making Processes
An accurate equipment cost calculator enhances decision-making by providing essential data at usersโ fingertips. With current and comprehensive cost information, forestry managers can evaluate different scenarios before making strategic choices. For example, they can assess whether to purchase new machinery or maintain existing equipment.
Being able to simulate different financial outcomes allows for a more informed approach. Using the spreadsheet, managers can run break-even analyses. They can determine when an investment will start yielding returns based on their unique operational costs and revenue projections.
Moreover, the dynamic nature of the calculator allows for quick adjustments. As new cost data becomes available, it becomes simple to update figures in real time. This flexibility makes the spreadsheet a responsive tool for continuous financial assessment, ultimately leading to more effective and timely decisions.
It is crucial to integrate the equipment cost calculator into regular financial reviews, so that adjustments can occur as market conditions shift.
Challenges in Equipment Cost Calculation
Cost calculation for equipment in forestry management poses unique challenges that can significantly impact resource planning and financial decision-making. Recognizing these challenges is crucial for forestry professionals who aim to optimize their operations. The predominant issues include data accuracy and dynamic market conditions, each requiring careful consideration to enhance the reliability of cost assessments.
Data Accuracy Issues
One of the foremost challenges in equipment cost calculation is ensuring the accuracy of data used within the cost calculator spreadsheet. Inaccurate data can lead to misguided financial decisions, affecting not only budgeting but also long-term investment strategies.
Key considerations include:
- Collecting Comprehensive Data: Gathering detailed information on equipment costs, including purchase prices, operating expenses, and maintenance costs, is essential. Missing or incorrect data points can skew the overall calculations.
- Regular Updates: Equipment costs are not static. They fluctuate due to various factors, including inflation, technological advancements, and changes in market demand. Regularly updating the data is crucial to maintain accuracy.
- Verification Processes: Establishing checks and balances in data entry can help mitigate human errors. Cross-referencing information from multiple sources aids in validating the reliability of the cost data.
"Accurate data collection is the foundation of sound financial decision-making in forestry management."
Enhancing data accuracy not only improves current assessments but also builds a stronger framework for future analyses.
Dynamic Market Conditions
Another significant challenge arises from the ever-changing market conditions. Equipment costs, influenced by economic trends and external factors, can vary widely, making cost estimation a complex task.
Several aspects to consider include:
- Market Volatility: Prices for machinery and equipment can fluctuate based on supply chain disruptions, economic downturns, or shifts in consumer demand. Such volatility demands that forestry managers remain vigilant and adaptable.
- Emerging Technologies: As new technologies are introduced, they can render existing equipment obsolete or change the cost structure of operations. Staying informed about industry advancements is essential for making educated decisions.
- Environmental Policies: Regulations aimed at enhancing sustainability can also affect equipment costs. Compliance with new policies may necessitate new investments or modifications to existing machinery.
Addressing dynamic market conditions involves adopting a flexible approach. Scenario modeling can prepare organizations for various economic situations, helping them navigate uncertainties more effectively.
Future Trends in Forestry Equipment Cost Management
Understanding future trends in forestry equipment cost management is essential for professionals in this sector. As the industry evolves, factors such as technological advancements and sustainability considerations play a pivotal role. Forestry management needs to adapt to these shifts to ensure efficient operations and cost-effectiveness.
Technological Advancements
Technological progress is transforming forestry operations. Innovations in equipment design and manufacturing are resulting in more efficient machines that operate at lower costs. Advanced data analytics and software tools, such as specialized equipment cost calculators, are becoming integral.
These calculators allow for precise tracking of equipment performance and costs over time, enabling managers to make informed decisions. For example, cloud-based platforms can provide up-to-date market data that helps in forecasting future costs and planning budgets effectively. With the implementation of IoT devices, real-time monitoring of equipment usage can reduce maintenance costs and improve overall efficiency.
Moreover, automation in forestry equipment is reducing labor costs while increasing productivity. The use of drones for surveying and monitoring forest health provides accurate data without significant manual effort.
In essence, embracing these technological advancements can yield substantial long-term savings and enhance the overall profitability of forestry management practices.
Sustainability Considerations
As environmental concerns grow, sustainability in forestry management becomes increasingly critical. The awareness of sustainable forestry practices affects equipment choices and cost management strategies.
Investing in eco-friendly equipment may entail higher upfront costs but often results in savings over time through lower fuel consumption and reduced emissions. Moreover, such investments align with global trends toward corporate social responsibility.
Considerations like using electric or hybrid machinery not only align with sustainability goals but also often provide tax incentives or grants. This shift towards green technology is not just a trend; it is becoming a fundamental component of successful forestry management.
Furthermore, adopting sustainable practices influences public perception and can enhance market competitiveness. Companies recognized for their commitment to sustainability may attract more clients.
"Investing in sustainability is not just an ethical choice; it is a strategic business decision."
Epilogue
In the field of forestry management, having a thorough grasp of equipment costs is essential. This article has explored how an equipment cost calculator spreadsheet serves as a crucial tool for professionals in the industry. The calculator's structured approach aids in making informed financial decisions that impact resource allocation and project viability.
Summary of Key Points
- Importance of Equipment Cost Calculation: Understanding the elements of equipment costs is vital for effective budgeting and long-term planning. Accurate assessments help avoid cost overruns and foster financial health in forestry operations.
- Components of a Cost Calculator Spreadsheet: A well-designed spreadsheet includes essential input fields, calculation formulas, and output sections. Each of these components plays a role in providing clear insights into equipment expenses.
- Practical Applications: From budgeting for projects to planning future investments, the calculator can be utilized in a variety of situations. Its applications extend to short-term needs as well as strategic long-term goals.
Final Thoughts on Cost Management in Forestry
Effective cost management is not merely about tracking expenditures; it is about fostering a deeper understanding of how these costs affect overall operations. As the forestry sector evolves, incorporating technology and sustainability considerations will be crucial. Utilizing an equipment cost calculator not only simplifies the financial aspect but also supports the broader objective of making forestry practices more sustainable.