CNC Timber Cutting Machines: Applications and Benefits
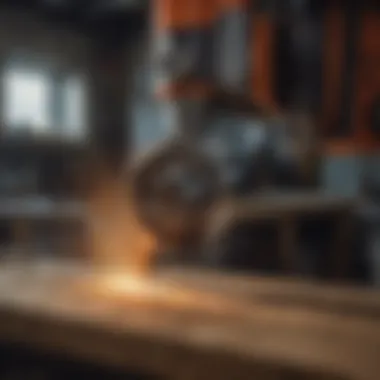
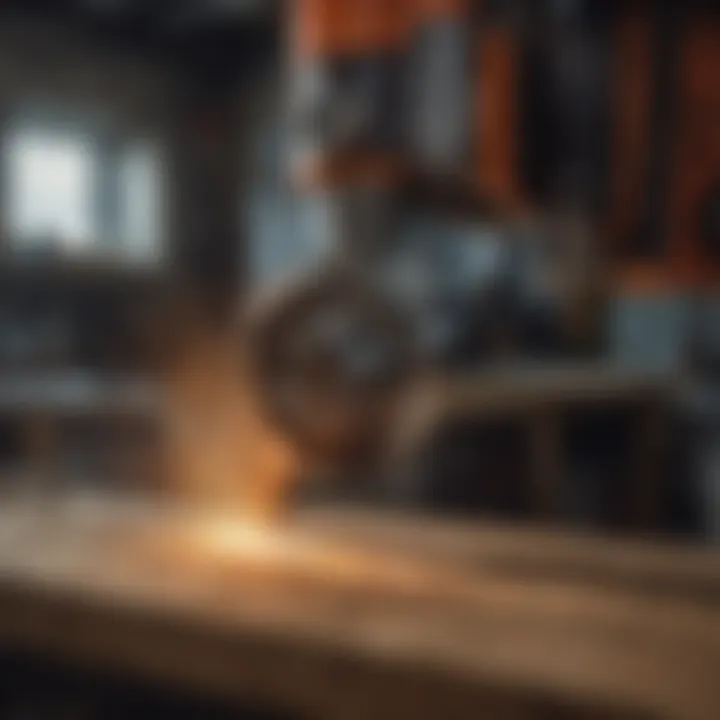
Intro
In recent years, the integration of technology in forestry and timber processing has seen significant growth. The CNC timber cutting machine exemplifies this trend, showcasing how advanced machinery can enhance operational efficiency and promote sustainable practices in the industry. This article aims to provide a comprehensive overview of CNC timber cutting machines, exploring their applications, benefits, and the technology that drives them. By understanding these machines, forestry professionals can better appreciate their impact on modern forestry and woodland stewardship.
Understanding Forestry Practices
Forestry practices encompass a variety of methods employed in the management of forests. The nuances of these practices can shape both environmental and economic outcomes.
- Types of Forestry Practices
- Historical Context: Understanding the historical development of forestry practices is crucial. Initially, timber was harvested using manual tools. As demand grew, mechanization started to transform the industry. Today, CNC machines represent the pinnacle of this evolution, offering precision and efficiency that were previously unattainable.
- Sustainable Forestry: Focuses on managing forest resources to meet present needs without compromising future generations.
- Selective Logging: Involves the careful removal of specific trees to minimize ecological impact.
- Clear-Cutting: Removing all trees in a designated area; a controversial practice that raises concerns about biodiversity.
- Agroforestry: Combines agriculture and forestry to create sustainable land-use systems.
Principles of Woodland Stewardship
Woodland stewardship emphasizes responsible management of forest resources. This approach seeks to balance ecological health and economic viability.
- Conservation Techniques: Effective techniques include controlled burns to reduce underbrush, replanting native species, and establishing protected areas, enhancing biodiversity.
- Managing Forest Resources: Modern technology, like CNC timber cutting machines, aids in optimizing resource management. These machines allow for accurate cuts, reducing waste and ensuring the longevity of forest resources. Emphasizing data-driven decision-making can also bolster resource management efforts.
Sustainable Forest Management
Sustainable forest management is increasingly recognized as important in meeting ecological and economic goals. It entails strategies that promote both environmental integrity and economic returns.
- Certification Standards: Organizations such as the Forest Stewardship Council (FSC) provide certification for sustainable practices. This adds credibility to timber products and can enhance market demand.
- Economic Benefits of Sustainability: Sustainable practices often lead to long-term cost savings. By minimizing waste and ensuring healthy forest ecosystems, businesses can achieve greater profitability while supporting environmental objectives.
"Efficient forestry practices not only protect our forests but also contribute positively to the economy. The role of technology is essential in achieving this balance."
To summarize, CNC timber cutting machines represent a significant advancement in forestry practices. They enable more efficient resource management, contribute to conservation efforts, and support sustainable economic practices. Understanding their role within the broader context of forestry and woodland stewardship is critical for professionals aiming to innovate and safeguard our natural resources.
Intro to CNC Timber Cutting Machines
CNC timber cutting machines play a crucial role in modern forestry and woodworking practices. As industries seek to enhance production efficiency while maintaining high standards of quality, these machines have emerged as indispensable tools. The integration of computer numerical control (CNC) technology in timber cutting facilitates precision, which is necessary for various applications such as furniture production, architectural components, and custom woodworking.
The importance of CNC timber cutting machines lies not only in their ability to cut timber with high accuracy but also their contributions to sustainable practices. These machines allow for optimized material usage, which translates into less waste—a significant consideration as environmental concerns grow within the industry.
Additionally, understanding CNC timber cutting machines offers insights into the broader context of technological advancements in forestry. Familiarity with both historical and modern technologies informs practitioners about best practices, cultivation of skills, and innovative approaches to timber processing.
Definition and Purpose
CNC timber cutting machines are specialized devices that utilize computer-assisted technology to automate the cutting and milling of wood. Their primary purpose is to enhance precision and efficiency in timber processing, which is vital for industries that rely on accurate cutting for their products.
Some of the key features include:
- Precision Cutting: CNC technology allows for intricate designs that human operators may find difficult to execute consistently.
- Increased Productivity: Automated systems reduce the time spent on cutting operations, allowing companies to focus on other aspects of their production lines.
- Reduced Waste: By optimizing cuts, these machines ensure that more of the timber is utilized effectively.
Historical Context
The evolution of timber cutting technology has undergone a significant transformation over the centuries. Traditional methods, relying heavily on manual labor, were replaced gradually by various mechanical devices starting in the 19th century. The introduction of electrical machines further streamlined the process but still lacked the precision achievable by CNC technology.
The real breakthrough came in the late 20th century when computer technology became affordable for many industries. This development led to the widespread adoption of CNC machines across multiple sectors, including timber cutting. Manufacturers realized the efficiencies gained by implementing such technology and began investing in more sophisticated CNC systems. Today, CNC timber cutting machines symbolically represent the intersection of craftsmanship and advanced technology, significantly impacting how timber is processed globally.
Understanding CNC Technology
CNC technology plays a pivotal role in the evolution of timber cutting machines. It stands at the intersection of precision engineering and computerized automation. This section explores its fundamentals, breaking down the elements and advantages that contribute to enhanced performance in timber operations.
What is CNC?
CNC, or Computer Numerical Control, refers to a technology where computers control machine tools. This process allows for the automation of complex cutting, milling, and engraving tasks. CNC technology replaces manual control with direct instructions given through programmed codes. This automation ensures higher quality results, as the machines operate with great precision.
Moreover, CNC technology has increased productivity across various industries, including forestry, by permitting continuous operation without the fatigue and errors associated with human operators. Programs can be saved and replicated, allowing for efficient production runs and custom design implementations without extensive setups.
Components of a CNC Machine
A CNC machine consists of several key components, which work together to achieve precise cutting results. Understanding these components is aimed to fully grasp how CNC machines function in the forestry sector.
Controller
The controller is the brain of a CNC machine. It interprets the program instructions and translates them into machine movements. A major characteristic of a CNC controller is its capability to handle complex calculations rapidly. This speed is essential because it affects how quickly a machine can execute moves and cuts.
Controllers can vary in sophistication, with options like Fanuc or Mac being popular in the CNC community. The unique feature of advanced controllers is their ability to integrate with different software systems, allowing for more flexible programming. However, the complexity of these systems can present a learning curve for new users.
Drive Systems
Drive systems are crucial for converting the controller's signals into actual movement. They consist of stepper motors or servo motors, which precisely control the position and speed of the cutting tools. Stepper motors are typically favored for simple applications due to their cost-effectiveness and reliability. Servo motors, while more expensive, offer greater accuracy and feedback capabilities.
The key feature of drive systems is their role in determining the speed and efficiency of cutting operations. Depending on the application, a system's choice can influence cycle times and the overall finish of products.
Cutting Tools
Cutting tools are the components that physically perform the cutting action in CNC machines. They are designed from materials like high-speed steel or carbide to enhance durability and longevity. One of the prominent characteristics of CNC cutting tools is the variety available, catering to different timber types and desired finishes.
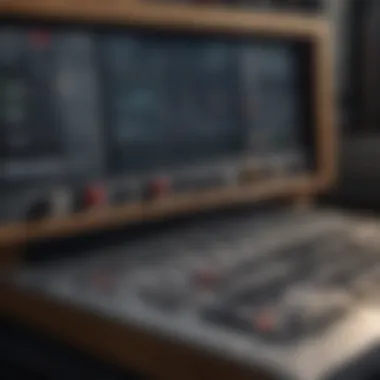
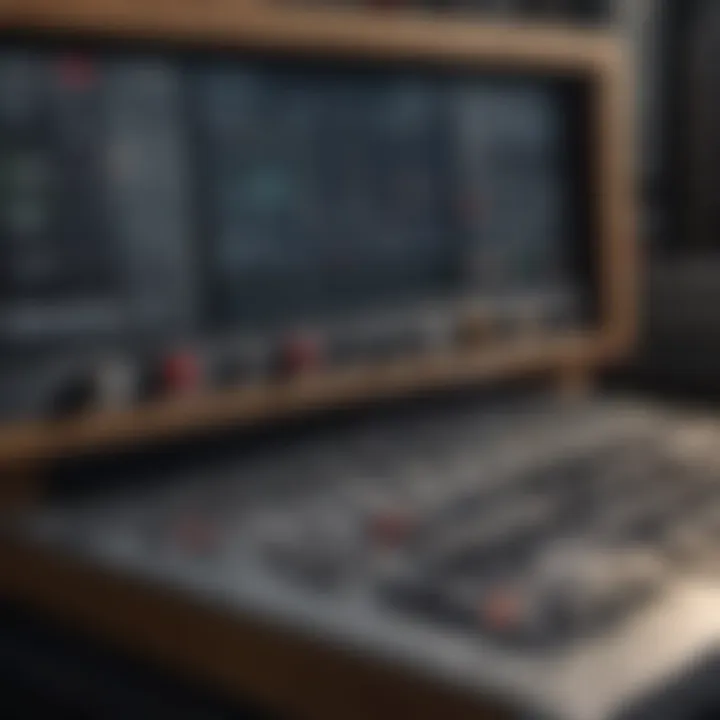
Specificity in tool selection can dictate the success of a project. For instance, specific tools are designed for softwoods, while others suit hardwood applications. However, the disadvantage can include increased costs, as the incorrect tool can lead to damage and waste.
"Understanding the core anatomy of CNC machines reveals the complexities behind their operation, and underscores the importance of each component in achieving desired outcomes in timber applications."
CNC technology revolutionizes timber cutting through its intricate workings and designed components. Understanding these systems and their interactions is essential to benefit from the efficiencies they offer in forestry.
Types of CNC Timber Cutting Machines
Understanding the types of CNC timber cutting machines is crucial in evaluating their diverse applications, benefits, and unique functionalities. Each type serves specific purposes, catering to different aspects of timber processing. Familiarity with these machines can significantly impact efficiency, quality, and sustainability within the forestry sector.
Router Machines
Router machines are one of the most widely used CNC timber cutting tools. They are particularly known for their versatility and precision in shaping and carving wooden materials. Router machines use a rotating cutting tool to remove material from the surface of the wood.
The application of router machines extends from simple cuts to complex designs, making them ideal for both professional woodworkers and hobbyists alike. The ability to program intricate patterns enhances design possibilities. Different bits can be utilized, which allow for various cutting styles and finishes.
Moreover, router machines are reletively cost-effective compared to other CNC machines. They often come with user-friendly software, making them accessible for users new to CNC technology.
Laser Cutters
Laser cutters represent another pivotal type of CNC machine in timber processing. These machines employ a focused laser beam to cut and engrave wood with extreme precision. The advantage here is the level of detail that can be achieved, which is particularly beneficial for intricate designs.
The laser cutting process involves minimal material waste, as it can make very fine cuts without the need for additional material removal. This efficiency can contribute to better sustainability practices in forestry. The heat generated by the laser also slightly seals the edges of the cut, which can enhance the finishing quality of wood.
Additionally, laser cutters can handle a variety of materials. They are not limited to wood but can also cut through acrylic, plastics, and some metals. This multi-functionality makes them an invaluable asset in workshops looking to diversify their production.
Plasma Cutters
Plasma cutters are less common in timber cutting but still play a role in specific applications. They are generally used for cutting thicker materials and resemble traditional cutting methods in some aspects. Plasma technology uses high-temperature plasma to cut through materials, which allows fast processing speeds.
For timber applications, plasma cutters are mostly found in companies engaged in designing large wood structures or in automotive industries where wood is used in combination with metal. Their capabilities to handle various thicknesses provide versatility, but they require careful handling due to the heat involved, which can warp or damage more delicate wood materials.
In summary, each type of CNC timber cutting machine possesses unique capabilities. Understanding these differences is essential for anyone involved in timber processing, from choosing the right machine for specific tasks to optimizing processes to adhere to sustainability goals.
Applications in the Forestry Sector
The application of CNC timber cutting machines within the forestry sector holds significant relevance. These machines enhance productivity, streamline processes, and support innovative wood processing techniques. As timber's demand increases, so does the necessity for precision and efficiency. Utilizing CNC technology aids in achieving these objectives, ensuring that timber-related businesses can meet market challenges effectively.
Precision Cutting
Precision cutting is one of the standout features of CNC timber cutting machines. They can execute cuts with a degree of accuracy that is unattainable through manual methods. This is crucial in applications where millimeter precision affects the overall quality of the finished product.
CNC cutting techniques enable the creation of complex shapes, intricate designs, and detailed patterns consistently. These machines operate based on digital designs, translating them into actual physical products without error or deviation. This level of precision not only enhances production quality but can also significantly reduce the need for rework and material waste.
For instance, a CNC router can precisely cut joints for furniture that fit perfectly, minimizing gaps and maintaining structural integrity. This reliability in production promotes higher customer satisfaction, fostering repeat business and trust in the brand.
Custom Woodwork Production
CNC timber cutting machines are essential for custom woodwork production. They allow artisans and craftsmen to take on unique projects without compromising on quality. Custom designs can be programmed directly into the machinery, enabling the rapid production of specialized items that meet specific client needs.
The versatility of CNC technology permits the manipulation of various wood types and sizes. From creating bespoke furniture pieces to architectural elements, these machines serve a wide array of applications. This adaptability not only fuels creativity but also allows businesses to diversify their offerings, appealing to a broader range of customers.
Also, custom woodwork production can be economically viable due to reduced turnaround times, making it feasible for small businesses to operate competitively. The ability to produce unique items efficiently gives craftsmen a considerable advantage in today's market.
Sustainable Practices
Sustainable practices are more than just a trend; they are a necessity in modern forestry. CNC timber cutting machines contribute to sustainability in several ways. For starters, their precision cutting capabilities minimize waste, ensuring that more raw material is converted into usable products. By optimizing material usage, companies can lower their ecological footprint.
Another aspect of sustainability relates to the type of wood processed. Many CNC machines can be programmed to work with reclaimed or sustainably sourced timber, allowing businesses to advocate for sustainable forestry practices. This approach aligns with global efforts to combat deforestation and promote responsible resource management.
Moreover, the automation provided by CNC technology reduces energy consumption compared to traditional methods. This efficiency is particularly notable in operations where high-volume wood cutting occurs, leading to both cost savings and a reduced environmental impact.
“By embracing CNC technology, the forestry sector not only meets consumer demands but also adheres to sustainable practices that benefit the environment.”
Benefits of CNC Timber Cutting Machines
CNC timber cutting machines offer distinct advantages that make them essential in modern forestry. Their ability to increase productivity and enhance the quality of wood products has revolutionized the industry. Understanding the benefits of these machines allows forestry professionals to assess their impact on operational efficiencies, precision work, and sustainability practices. In this section, we will explore three primary benefits: increased efficiency, consistency and accuracy, and waste reduction.
Increased Efficiency
One of the most prominent benefits of CNC timber cutting machines is their capability for increased efficiency. Unlike traditional cutting methods, CNC machines automate the cutting process. This automation speeds up production, allowing for a larger volume of work to be completed in less time.
For example, operators can program various cutting tasks, which means that after an initial setup, the machine can perform multiple operations without the need for continuous human input. Routine cuts or complex designs can be completed swiftly, minimizing downtime. The advanced software integrated into these machines also optimizes cutting paths, which furthers operational efficiency.
Increased efficiency translates to higher output quality in a shorter time, making CNC machines a game changer in the forestry sector.
Consistency and Accuracy
CNC timber cutting machines excel in providing consistency and accuracy. Unlike manual cutting, where human error can lead to discrepancies, CNC systems operate based on precise coordinates and measurements. This results in identical cuts across multiple pieces, which is crucial for projects requiring uniformity.
The precision of CNC cutting is essential in custom woodwork production. It allows artisans and manufacturers to create intricate designs with high accuracy. Accurate cuts not only enhance aesthetic appeal but also ensure that fitted parts interlock correctly, reducing the need for adjustments during assembly. This level of accuracy contributes to overall project quality, as each component aligns perfectly with design specifications.
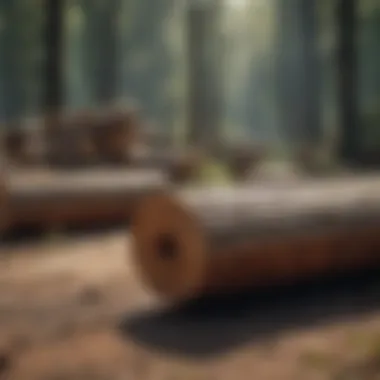
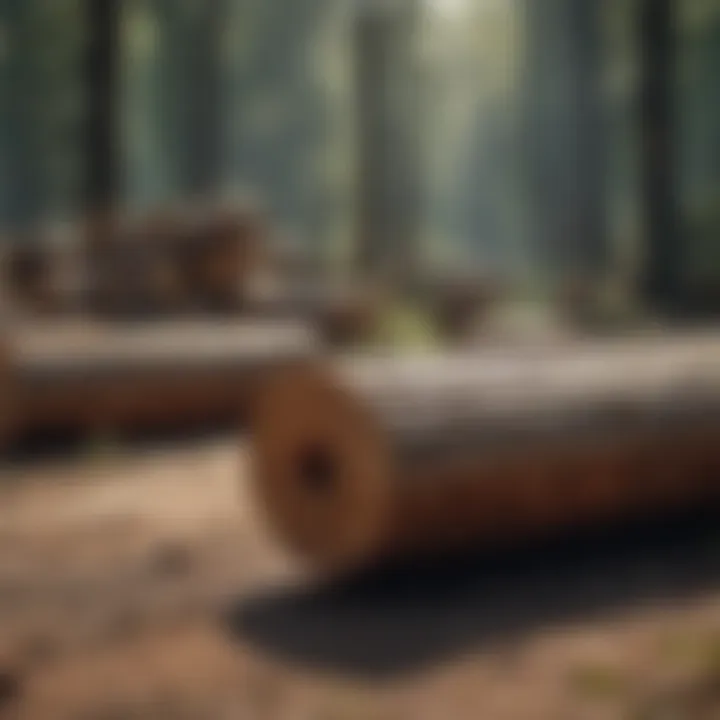
Waste Reduction
Another significant advantage of CNC timber cutting machines is their potential for waste reduction. Efficient material usage is a critical consideration in the forestry sector, where raw materials can be limited. CNC machines allow for detailed planning and execution, which helps minimize offcuts and scrap material.
By optimizing cutting layouts, manufacturers can make the most out of each timber piece. This not only conserves resources but also has a positive environmental impact. Reduced waste means fewer trees are needed for the same output, aligning with sustainable forestry practices.
In summary, the benefits of CNC timber cutting machines extend beyond operational enhancements. They foster a greater commitment to quality, precision, and environmental responsibility in the forestry industry.
Technical Considerations
Understanding the technical considerations of CNC timber cutting machines is essential for optimizing their use and ensuring effective operations. Technical considerations encompass both the software requirements needed for operation and the maintenance practices that keep machines running smoothly. When deployed correctly, these aspects can greatly enhance the productivity and longevity of CNC timber cutting machines.
Software Requirements
The software utilized in CNC timber cutting machines is pivotal to their functionality. It connects the operator's intentions with the machine's capabilities. Common software includes CAD and CAM, which help in crafting precise designs and executing them effectively.
Key software types include:
- CAD (Computer-Aided Design): This helps create detailed drawings and models. It is crucial for planning the design before cutting begins.
- CAM (Computer-Aided Manufacturing): This generates the necessary instructions for the CNC machine to cut the timber as intended.
It is important that forestry professionals choose software that aligns with their specific cutting needs. Compatibility with the CNC hardware must also be ensured, as discrepancies can lead to inefficiencies.
"Selecting appropriate software is just as important as the machinery itself; it can be the difference between a smoothly run operation and costly errors."
Maintenance Practices
Regular maintenance is key to prolonging the life of CNC timber cutting machines. These machines consist of several intricate components that require attention to detail. A well-maintained machine operates efficiently, which can result in significant cost savings over time.
Effective maintenance practices include:
- Regular Inspections: Routine checks can identify potential issues before they become major problems.
- Cleaning: Removing debris and dust from the machine helps prevent malfunctions and ensures precision cutting.
- Lubrication: Keeping moving parts well-lubricated can reduce wear and tear and improve the machine's performance.
- Software Updates: Ensuring that software is up-to-date is crucial for security and compatibility with new cutting technologies.
Incorporating a robust maintenance schedule ensures that CNC timber cutting machines perform optimally, thus maximizing their efficiency and effectiveness in various forestry applications.
Operational Guidelines
Understanding the operational guidelines for CNC timber cutting machines is vital for maximizing their efficiency and ensuring safety in the workplace. These guidelines provide a structured approach to setting up the machines, executing cutting tasks, and maintaining a safe work environment.
Setup Procedures
Setting up a CNC timber cutting machine involves several essential steps that must be carefully followed. This ensures the machine operates correctly and achieves the desired cutting results. The first step is to ensure the workspace is clear and adequately organized. A well-organized work area reduces hazards and improves productivity.
Next, the CNC machine should be placed on a sturdy and level surface. This stability is crucial, as an uneven setup can lead to errors during cutting. Connecting the machine to the power supply is next, followed by running pre-start checks. This includes checking for any visible damages, ensuring proper connections, and verifying fluid levels in hydraulic systems, if applicable.
After that, the material to be cut should be securely affixed to the machine's bed. It is important that the material remains stationary during the cutting process. Various clamps or fixtures can be employed for this purpose. Once the material is positioned, the operator needs to load the cutting program into the controller.
In this phase, operators must verify that the correct tools and cutting parameters are set. They should also conduct a dry run. A dry run is a simulation where the cutting tool moves without actually cutting. This allows operators to identify potential issues before the actual cutting begins.
Safety Measures
Safety is paramount when operating CNC timber cutting machines. The machinery, while advanced, does pose inherent risks such as moving parts and flying debris. Operators must wear appropriate personal protective equipment, which includes safety goggles, gloves, and steel-toe boots.
It is also essential to maintain a clear line of sight during operation. This ensures the operator can monitor the cutting process and quickly respond to any unexpected changes, such as tool malfunctions or material movement.
Understanding the machine's emergency stop procedures is necessary. Operators should know how to quickly halt the machine in the event of an emergency. Regular safety drills can help reinforce these emergency responses.
Another important safety practice is to avoid distractions. Focus while operating the machine helps reduce the likelihood of accidents. Additionally, operators should ensure that all safety guards and covers are in place before engaging the machine.
In summary, following the operational guidelines for CNC timber cutting machines enhances efficiency and ensures safety. Proper setup procedures and strict adherence to safety measures are critical components of successful machine operation.
"Safety is not just a priority; it is a fundamental practice for any CNC operation."
By implementing these guidelines, forestry professionals can optimize the benefits of CNC technology in timber industries.
Future Trends in CNC Timber Cutting
The realm of CNC timber cutting machines continues to evolve. Staying updated on future trends is crucial for professionals engaged in forestry and woodworking. These trends highlight advancements that not only enhance efficiency but also support sustainability and innovation in practices. The integration of technology influences how timber is processed, ensuring that the industry remains competitive and environmentally responsible.
Advancements in Technology
Rapid advancements in technology contribute notably to the CNC timber cutting sector. Recent innovations involve improved computing power and software applications. This enhancement grants users greater precisions during cutting processes.
- Enhanced Software Solutions: New software allows for more complex designs and operations, leading to higher productivity and ease of use.
- Improved Cutting Tools: Developments in material science have introduced cutting tools that last longer and offer better performance, reducing maintenance costs.
- High-Speed Cutting Techniques: The emergence of high-speed cutting technology increases processing speeds significantly without compromising quality.
These factors collectively lead to faster production turnaround times and optimization of resource use. Such advancements not only benefit manufacturers but also empower them to meet the growing consumer demand for custom wood products.
Integration with AI and Automation
The integration of artificial intelligence and automation systems into CNC timber cutting machines represents a transformative shift. AI algorithms facilitate smarter machine operations, optimizing cuts based on the specific characteristics of the timber used. Automated systems allow machines to self-adjust based on real-time data, enhancing both the efficiency and safety of operations.
- Predictive Maintenance: AI helps predict when a machine might fail, enabling proactive measures to prevent unplanned downtime.
- Adaptive Learning: As these systems operate, they learn from the data collected, continuously refining their processes for better output.
- Streamlined Production Processes: Automation reduces the need for manual intervention, leading to a smoother workflow and higher output.

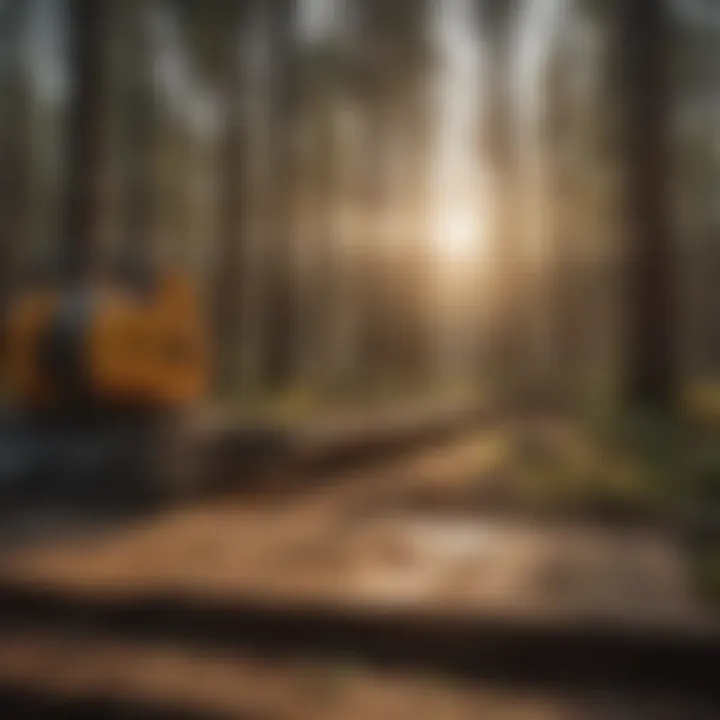
Integrating these advancements into current practices not only improves operational efficiency but also promotes sustainable forestry practices by minimizing waste and ensuring precision in cuts.
In summary, future trends in CNC timber cutting are crucial for promoting efficiency and innovation. The continual evolution of technology responds to both market needs and environmental standards, marking a promising path forward for the industry.
Staying abreast of these trends will equip professionals in forestry and related sectors with the knowledge necessary to implement best practices and capitalize on technological innovations.
Case Studies and Examples
Understanding the practical applications of CNC timber cutting machines is essential for grasping their significance in the forestry sector. By analyzing case studies and providing relevant examples, we can illustrate how technology transforms operations in this industry. These real-world insights highlight both benefits and challenges, offering an avenue for knowledge sharing among forestry professionals and academics.
Industry Applications
CNC timber cutting machines find applications across various segments in the forestry sector. These tools are not limited to just one type of production; they enhance operations in several ways:
- Furniture Manufacturing: The accuracy of CNC machines allows for the production of intricate designs that would be labor-intensive when done manually.
- Architectural Elements: Custom woodwork, like beams and moldings, benefits from precise cuts that match architectural specifications.
- Construction: Efficiently cutting materials such as plywood and lumber ensures timely project completion. This is critical in industries where delays can lead to escalating costs.
Each of these applications showcases the versatility of CNC technology. Businesses leveraging this technology often report improved output rates and reduced lead times.
Successful Implementation Stories
Successful implementation stories exemplify how different companies integrate CNC timber cutting machines into their operations. These narratives resonate within the forestry industry, inspiring others to adopt similar practices. Consider the following examples:
- Company A: A furniture manufacturer that adopted a CNC router machine. The switch allowed them to double production speed while maintaining high-quality standards. The owners noted that the upfront investment paid off in less than two years due to increased sales volume.
- Company B: This architectural woodworking firm implemented CNC technology for custom moldings. After noticing a high demand for unique designs, they utilized a CNC laser cutter to produce items that impressed clients. Their precision cuts reduced material waste, enhancing sustainability.
"Transitioning to CNC technology has allowed us to tackle more intricate orders. It’s not just about speed; it’s about meeting client expectations in quality and design." - Owner, Company B
- Company C: A contractor specializing in residential builds used CNC plasma cutters to streamline their cutting process. Their ability to deliver materials with precise cuts led to fewer errors on-site, resulting in both cost savings and satisfied customers.
These stories underscore not just the technical benefits but also the transformative impact on business operations. As companies adapt to new technologies, they pave the way for innovation in the forestry sector. By discussing these case studies and real-life applications, this article aims to offer valuable insights for forestry professionals looking to enhance their operations with CNC timber cutting technology.
Comparative Analysis with Traditional Methods
The examination of CNC timber cutting machines against traditional methods is central to understanding their overall impact in the forestry sector. This analysis sheds light on multiple dimensions, including economic factors, production capabilities, and quality control.
Cost Analysis
One of the fundamental aspects of the comparative analysis lies in the cost implications of using CNC timber cutting machines versus traditional cutting techniques. Traditional methods usually involve manual labor, which can be costly in terms of wages and inconsistent output. In contrast, CNC machines offer a higher degree of automation, significantly reducing labor costs over time. While the initial investment in CNC technology can be substantial, the long-term savings from decreased labor and increased efficiency often justify this expense.
- Machinery Costs: CNC machines may range considerably in price, influenced by features and capabilities. However, the return on investment becomes apparent when considering increased production speeds.
- Labor Costs: Automation leads to fewer workers being needed, which can drastically cut costs in industries focused on mass production.
- Material Wastage: CNC machines precisely cut materials, reducing offcuts and rework costs, unlike traditional methods where human error can lead to excess trimming and adjustments.
Quality Outcomes
The quality of timber cut by CNC machines often surpasses that achieved through traditional methods. CNC technology provides a level of precision that human operators can rarely match. This improvement in quality translates into several practical benefits:
- Consistent Measurements: CNC machines operate according to programmed specifications, ensuring uniformity in each piece produced. In contrast, variations often occur with manual cutting methods due to inconsistent human input.
- Finish Quality: The ability to use various tooling options enhances the finishing quality of components. CNC machines can implement specialized cutting tools that produce smoother edges compared to traditional saws.
- Customizability: CNC allows for complex designs that would be difficult or impossible to achieve by traditional means. This versatility ensures that businesses can meet precise client specifications with greater ease.
"Elevating cutting precision is not just about speed; it’s about redefining the capabilities of wood finishing through technology."
In summary, comparing CNC timber cutting machines with traditional methods reveals significant advantages in cost-effectiveness and quality outcomes. While initial costs can be daunting, the potential for increased efficiency, reduced labor expenses, and superior quality makes CNC technology a worthwhile investment for forestry professionals.
Environmental Impact Considerations
Understanding the environmental impact of CNC timber cutting machines is crucial in today’s context of sustainable industrial practices. As these machines become prevalent in the forestry sector, it is imperative to assess their ecological implications. The application of CNC technology in timber cutting can offer distinct advantages concerning sustainability, resource management, and waste reduction. Promoting responsible usage and efficiency not only benefits businesses but also conserves natural resources and preserves ecosystems.
Sustainability Metrics
Measuring sustainability within the realm of CNC timber cutting involves various metrics that reflect environmental performance. Quantifiable indicators include:
- Energy Consumption: Assessment of energy used during operation. Lower energy usage implies reduced carbon emissions, favoring environmentally friendly practices.
- Material Efficiency: Analyzing the ratio of wood utilized versus waste produced. Higher material efficiency means less spoilage and maximizes the yield from each timber batch.
- Lifecycle Assessment (LCA): Evaluating the environmental impact of the machine from production to disposal is key. The LCA highlights areas for reducing footprints and improving sustainability.
By using these metrics, companies can benchmark their performance against industry standards. This allows for proactive adjustments to enhance overall environmental impact.
Waste Management Strategies
Effective waste management is pivotal when utilizing CNC timber cutting machines. Strategies for minimizing waste and enhancing recycling include:
- Optimized Cutting Patterns: Computer software can create cutting plans that minimize leftover materials. This reduces unnecessary waste and improves yield.
- Reuse of Offcuts: Leftover wood pieces from cutting operations can be repurposed or sold. This practice not only reduces waste but can also create added revenue streams.
- Recycling Programs: Implementing recycling initiatives can promote the use of salvaged wood, lessening the need for new materials. Recycling wood enables the reduction of pollution and resource depletion.
"Implementing effective waste management in CNC timber cutting promotes not just profitability, but also environmental responsibility and resilience in forestry practices."
Addressing environmental impact considerations in the use of CNC timber cutting machines promotes an awareness that transcends profitability, grounding operations within a framework of sustainability. By focusing on sustainability metrics and adopting waste management strategies, businesses can both protect natural resources and improve their operational efficiency.
Closure
In concluding this exploration of CNC timber cutting machines, it is essential to reflect on their significance in modern forestry and woodworking practices. The capabilities offered by this technology extend well beyond mere cutting efficiency. They provide a multitude of benefits that are valuable for both economic and environmental considerations. This article highlights these aspects, while also discussing the potential for future innovation in your field.
Summary of Key Points
The key points addressed in this article illustrate the multifaceted nature of CNC timber cutting machines:
- Efficiency Gains: These machines enhance production rates and reduce manual labor.
- Precision: CNC technology offers superior accuracy, leading to high-quality outputs with less material waste.
- Sustainability: The integration of CNC machines can contribute significantly to sustainable forestry practices.
- Technological Advancements: From software updates to hardware enhancements, there is an ongoing evolution in CNC technologies that continues to improve their functionality.
Looking Ahead to Innovation
Looking to the future, the impact of emerging technologies on CNC timber cutting machines will likely grow. The integration of artificial intelligence, for instance, has the potential to revolutionize how these machines operate, allowing for even more sophisticated design options and process optimizations.
In addition, future trends may include strengthened efforts toward automation, which could lead to further enhancements in productivity and efficiency. Keeping abreast of these developments will be critical for forestry professionals, ensuring your practices remain competitive and aligned with industry standards. Innovation in this field will not only benefit individual operators but also contribute positively to the broader goals of environmental sustainability and resource management.